Optimize Returns Management with Kitting & Consolidation
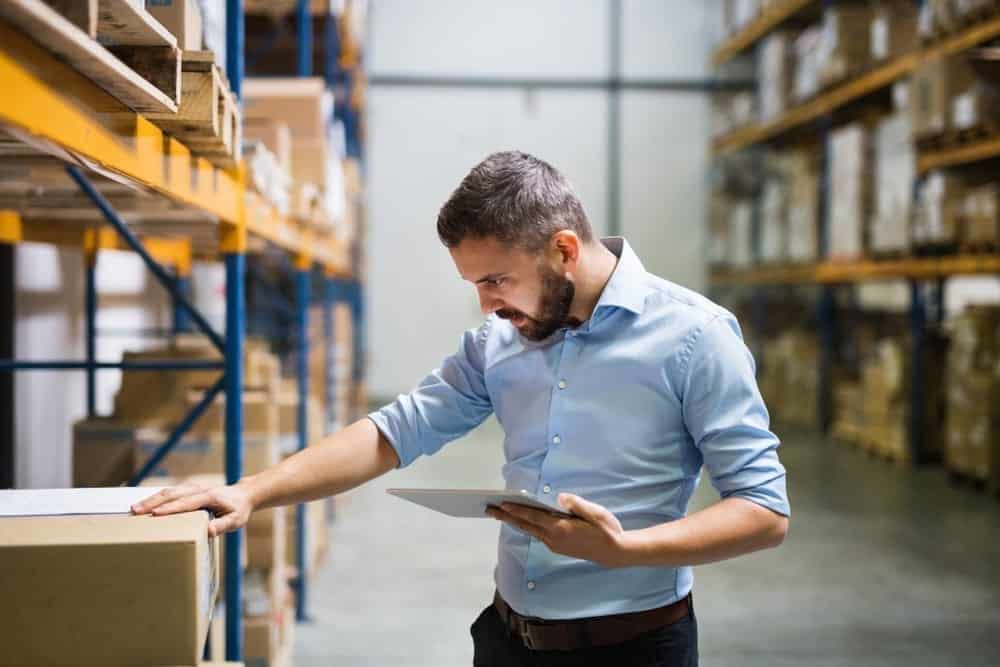
Kitting and consolidation is often discussed in the context of forward logistics, but it’s just as important in reverse logistics. When an item is returned, many pieces and components may need to be kitted and assembled if the item has to be repaired, refurbished or resold. Here’s what you need to know about the importance of efficient kitting and consolidation for returns management.
What is Kitting & Consolidation?
Kitting and consolidation services bring unfinished components together in a single place to assemble and ship. In the context of retail reverse logistics and returns management, this means bringing together parts for repair or refurbishment of a returned item. The item can then be returned or resold, giving the retailer some recouped value.
The Benefits of Kitting & Consolidation Software for Warehouses
Whether you manage returns yourself or use a 3PL provider, ensuring your returns management technology performs kitting and consolidation will improve efficiency and speed of the product’s exchange or resale. Here are three reasons your returns management system (RMS) should feature kitting and consolidation.
Maximize space
Using kitting and assembly services to keep component inventory together will significantly reduce the amount of space you need to store parts, packaging, trash, and other items. As you grow, you don’t want to take up valuable warehouse space in your facility to keep all these items onsite, which can be costly, especially if you have to add more warehouse facilities or undertake other capital-intensive projects to house these goods.
Improve productivity and efficiency for resale
The ability of your RMS to support kitting and consolidation will also support how quickly and efficiently you get items back on the shelf or send to a third-party recommerce site. Teams won’t spend an extra second hunting down parts, pulling them, and logging them.
This RMS use case is common among our electronics customers: Let’s say an electronics company received a return. It’s a server with a bad memory that can be repaired and is under warranty. Using ReverseLogix, warehouse employees can update the memory component with a different serial number and track it across other supply chain software systems before returning it to the customer. This is far more than what warehouse management software can deliver for returns management.
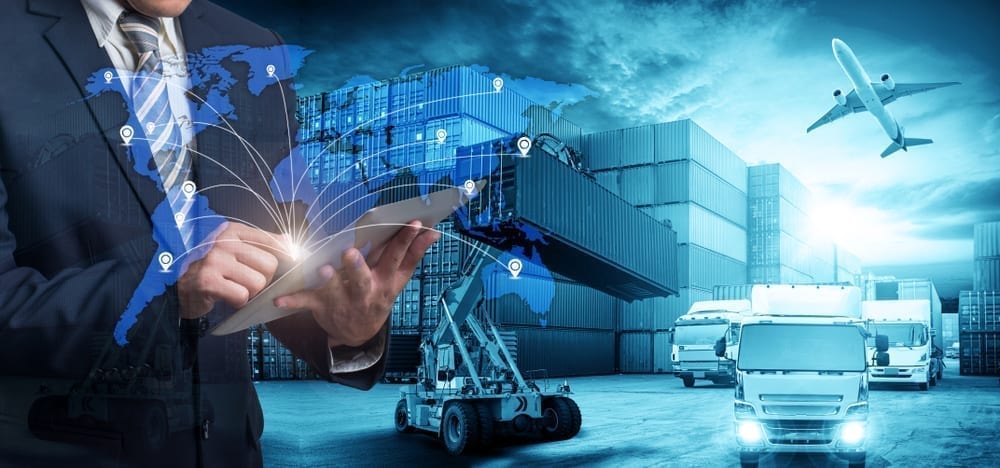
Inventory and parts tracking
Kitting and consolidation tools provide real-time tracking and reporting about product returns, so you can accurately track the use, status and ordering of parts. With in-depth data on your returns, you can better understand recovery costs and how to connect returned inventory to the right channels. This includes:
- Tracking of each part
- Age of each part
- Value of the part as it’s used in the repairs cycle
- Parts harvesting to leverage parts of unsold items
- Which items are returned at what rates
- Common reason codes, so you can uncover parts that may be faulty
Fewer than one-third of retailers state that they have visibility of all related returns management costs when it comes to loss in inventory value in storage.
Gartner
Global supply chains
Kitting and consolidation services help you manage the flow of materials as they are turned to your warehouse or DC, and find the most cost-effective and sustainable use for each component – anywhere in the world, and even across owned facilities or 3PL partners.
The Significance of Kitting & Consolidation for Returns Management
As companies seek to reduce cost and waste, repairs have become especially important for high-end market sectors like electronics, designer footwear or luggage. Returns management technology that facilitates kitting and consolidation for repairs and refurbishment will improve your parts management, automation and consistency.
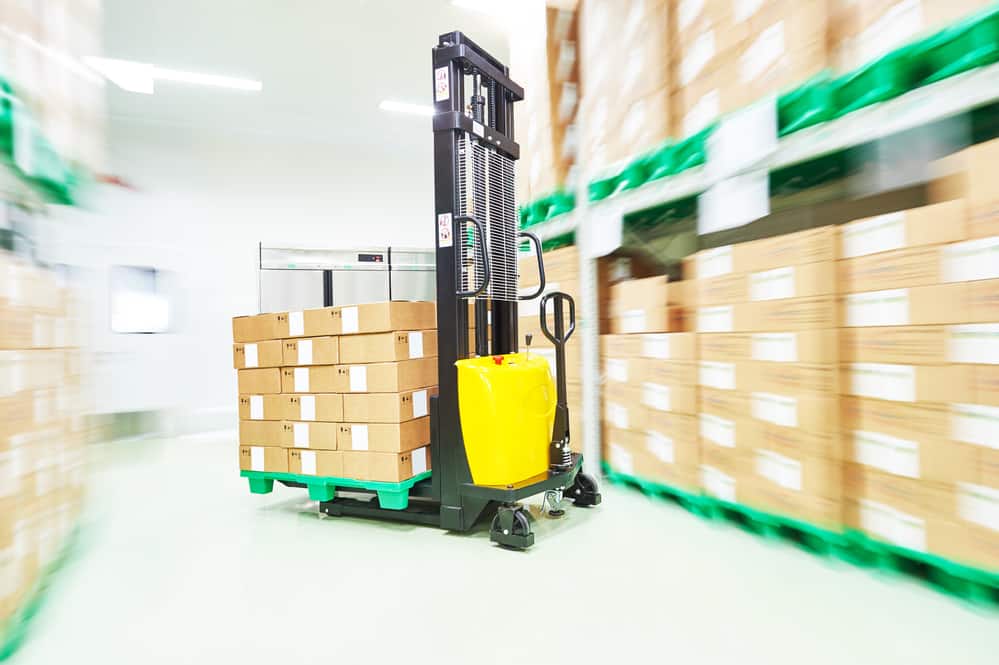
ReverseLogix Kitting & Consolidation Solutions Can Help You
The ReverseLogix RMS helps you manage complex repairs or refurbishments with kitting and consolidation solutions flexible to your specific needs.
By fully integrating with existing enterprise applications, ReverseLogix streamlines and coordinates end-to-end returns and repairs process, including:
- Configurable workflows based on your needs and products
- Warranty-based repairs
- Multi-level repairs
- DIY customer repairs
- Parts management
- Testing integration
- Billing code customization
“ReverseLogix allows us and Samsonite to track what parts may need more attention than others, what parts are used more, what parts may be more defective than other parts. It allows us to prepare for what’s coming next. If we’re aware of a specific part that needs more repair than others, we order that ahead of time so we’re ready to go once the consumer ships their product into us.”
Daniel Tsveer, Peter & Sons Luggage Service, a high-volume Samsonite repair center
Simplified returns
A dedicated returns management system streamlines and orchestrates service at all levels. Employees understand the repair needed based on the billing code. The system shows them which parts are needed, the repair workflows to execute, payment processing, and more.
- Perform repairs at multiple depot levels and stock transfer the repairable units to each level.
- Empower third-party repair centers such as 3PLs, after-sales care providers or remote repair centers anywhere in the world to work from the same workflows and standards.
- Get visibility into inventory, repairs data, diagnostics and reports across your network.
Enhanced recommerce programs
If you’re considering a recommerce program, ReverseLogix RMS is the must-have technology foundation of it. We support a variety of recommerce programs, including trade-ins, refurbishment, recycling and resale. Because we integrate with your other core supply chain software, we can be your one source for managing returns, tracking parts and getting in-depth data for smart recommerce decisions that benefits your company, customers and the planet.
Cost reduction
As production costs rise and supply chains clog, repaired items keep costs low by avoiding the need to produce an entirely new item. Get more value from a return and maximize its saleable value—whether it goes back to the customer or to inventory for another buyer.
Improved customer experiences
Build customer confidence in your brand with a service that fixes their item quickly and expertly. Sustainability in the retail industry is a growing concern among consumers: 80% of Gen Z has bought pre-owned goods and the secondhand fashion market is expected to grow 127% by 2026. That means reusing, recycling and reselling will continue growing in importance among your customer base.
Scalability and flexibility
ReverseLogix is the only RMS purpose-built for B2C, B2B and hybrid operations. The policy and rules engine is configurable and changeable to meet your policies, claims rules, vendor entitlements and approval hierarchies. Customize your own branded portal for customers to start returns, check a status and get notifications. Guide your team’s workflows for receiving, inspecting, and grading product returns to speed up and streamline processing.
“I can plan my manpower for the day or week, because all I need to do is look on ReverseLogix and it’ll tell me how many returns we’re expecting between my two different areas of returns.”
Erin Johnson, senior returns and vendor compliance manager, Genesco
Frequently Asked Questions
What is an Example of Kitting in Returns Management?
When items such as electronics are returned, there may be a need to repair or refurbish the product. Kitting and consolidation technology for returns will manage the workflows, parts, inventory and warranty considerations needed to handle these returns. Learn more about returns management.
What is the importance of kitting in returns & returns technology?
It’s important for any returns technology to also offer kitting and consolidation capabilities. As return volumes increase, so do the opportunities for repairing and selling the returned items. A single returns management platform that orchestrates the entire returns process, from start to finish, will give you the tools, data and ability to help your teams work with ease. For more information, see our RMS Buyer’s Guide.
What is the full kitting process?
For returns management, the full kitting and assembly process gathers the parts that go into repairing or refurbishing a returned item. Get a demo of how ReverseLogix can meet your kitting needs!