Returns Management vs Reverse Logistics: Understanding The Difference
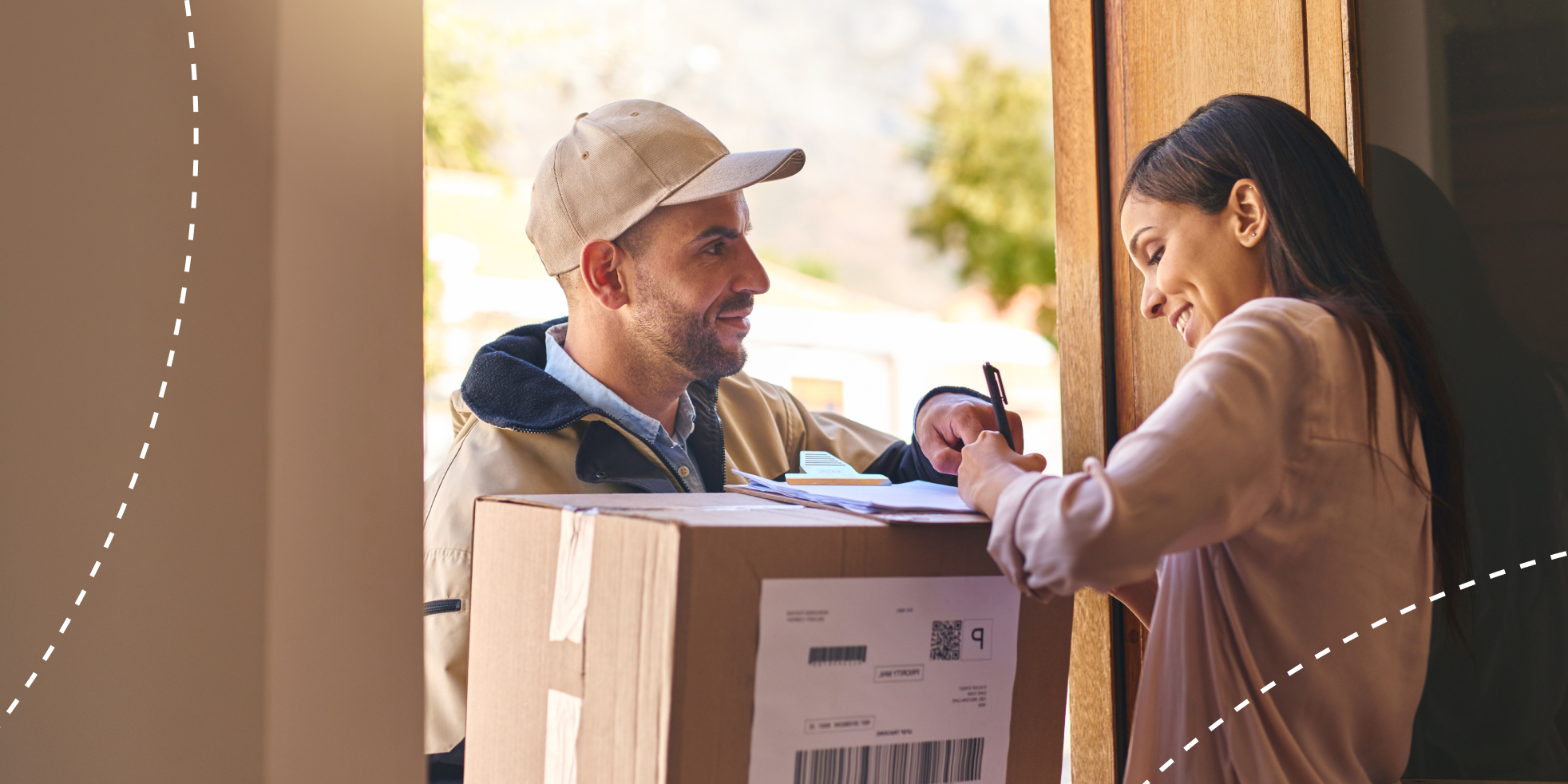
While often used interchangeably, reverse logistics and returns management are distinct, and yet both are pivotal in the same logistics process. About 30-35% of online purchased products will be returned. Brick-and-mortar shops have it at 9%. Understanding the difference between the two will go a long way to shaping the customer returns operation of a business or supply chain.
Reverse logistics involves the return of goods from consumers to the supply chain, while returns management plays a crucial role in ensuring a seamless consumer experience throughout the returns process. This process encompasses all the necessary steps to make the return process hassle-free for the consumer.
By understanding and effectively implementing these strategies, businesses can reduce costs and enhance customer satisfaction, leading to long-term success. By exploring the differences between the two, we explain why they are important and how businesses can optimize both logistics processes.
What is Reverse Logistics?
As the name implies, reverse logistics roughly ‘reverses’ the traditional logistics process. We have been used to seeing the flow of goods from the supply chain to the consumers. We now have a fast-growing industry where supply chains collect goods from consumers.
There are many reasons for this. The primary reasons are repair, refurbishment, recycling, unwanted products, and the sale of pre-owned products back to the business in question.
The process of managing the flow of goods from the consumer back to the supply chain is reverse logistics.
What Role Does The Reverse Logistics Play in Modern Supply Chain Management?
Reverse logistics has been pivotal to modern retail operations, especially following the dot-com boom. This was when online retailers, e-commerce, online marketplaces, and supply chains emerged. Reverse logistics provided a way for online retailers to woo customers by assuring them the possibility of returning an order if it does not meet their expectations.
Over time, the process has expanded to include avenues where customers can do more than just return products, like processing returns for repairs and selling preowned items. Modern reverse logistics strategies are specifically designed to efficiently process returns, utilizing unique return portals and data analytics to optimize the returns process. In the modern logistics and supply chain landscape, the reverse logistics process is leveraged in many ways:
Product Returns
Reverse logistics ensures the efficient handling, coordination, and control of the entire product return process. It could be from end customers, retailers, or other supply and distribution chain parties.
Recovery and Value Maximization
The reverse logistics operation focuses on recovering value from returned goods. It could do this through refurbishment and recycling. In situations where the supply chain cannot use the goods or products, it finds sustainable ways to dispose of the product.
Sustainability and Corporate Responsibility
Sustainability is no longer an option but a necessity for modern supply chain management. Reverse logistics provides supply chain operations a path to contribute positively to the environment. It allows for the proper disposal of goods, elongates the lifespan of products, and reduces greenhouse emissions across the board.
Continuous Improvement
The entire reverse logistics process is a great data source for customer feedback and measuring key performance indicators across the logistics chain. Businesses and supply chains prioritize how consumers feel about their operations and return processes. They analyze returns data to determine why, how, and when they return orders and other goods for repairs, sales, and disposal.
This way, the business and supply chain can gain insights that allow for continuous improvement of the entire system.
What is Returns Management?
Although reverse logistics deals with the return of goods from the consumer to the supply chain, it will be a nightmare without returns management. The returns management process ensures the proper handling of this return process to ensure the consumers are better off.
Returns management is consumer-centric. It entails the process of handling or managing all unwanted products sent back to the supply chain or business. The returns management operation ensures that the customer has an easy time. It focuses on providing a seamless and hassle-free return process for consumers.
This is how the reverse logistics process can ensure customer satisfaction.
What Role Does Returns Management Operation Play?
The returns management operation is designed to efficiently process returns, leveraging technology to optimize the returns process and minimize associated costs such as shipping, restocking fees, loss of sales, administrative expenses, and reputation damage. It streamlines the entire reverse logistics process by effectively managing returns, ensuring customers have a seamless experience.
Here is the role of the returns management operation.
Customer Satisfaction
As discussed earlier, it is a strategy that allows online retailers to assure the consumers of their genuineness. “Buy, and if you don’t like it, you can return it.” Effective returns management is a key component of a positive customer experience. It entails having a dedicated customer service team that ensures timely refunds and transparency throughout the entire process. This can also engender customer loyalty.
Cost Reduction
Through the returns management operation, businesses and their supply chains can minimize the financial impact of the reverse logistics process. It can accomplish this by streamlining the entire process to minimize transportation and handling costs through technology solutions like ReverseLogix.
The returns management operation also allows the supply chain to maximize the recovery of returned goods through optimized handling operations that allow for seamless refurbishment, recycling, and resale.
Inventory Management
When done properly, the reverse logistics process can help optimize and manage inventory by facilitating return, restocking, and redistribution. This allows the supply chain to minimize excess inventory and stockouts. It provides the supply chain with real-time updates on the state of the inventory of each SKU and where they are in the consumer-supply chain journey.
Regulatory Compliance
Many industries have regulations regarding logistics management, product returns and disposal, and sustainability guidelines. Effective returns management operations ensure supply chains and businesses can manage the reverse logistics process to comply with these regulations. This way, they can withstand scrutiny and avoid potential fines or penalties.
What is The Key Difference Between The Two?
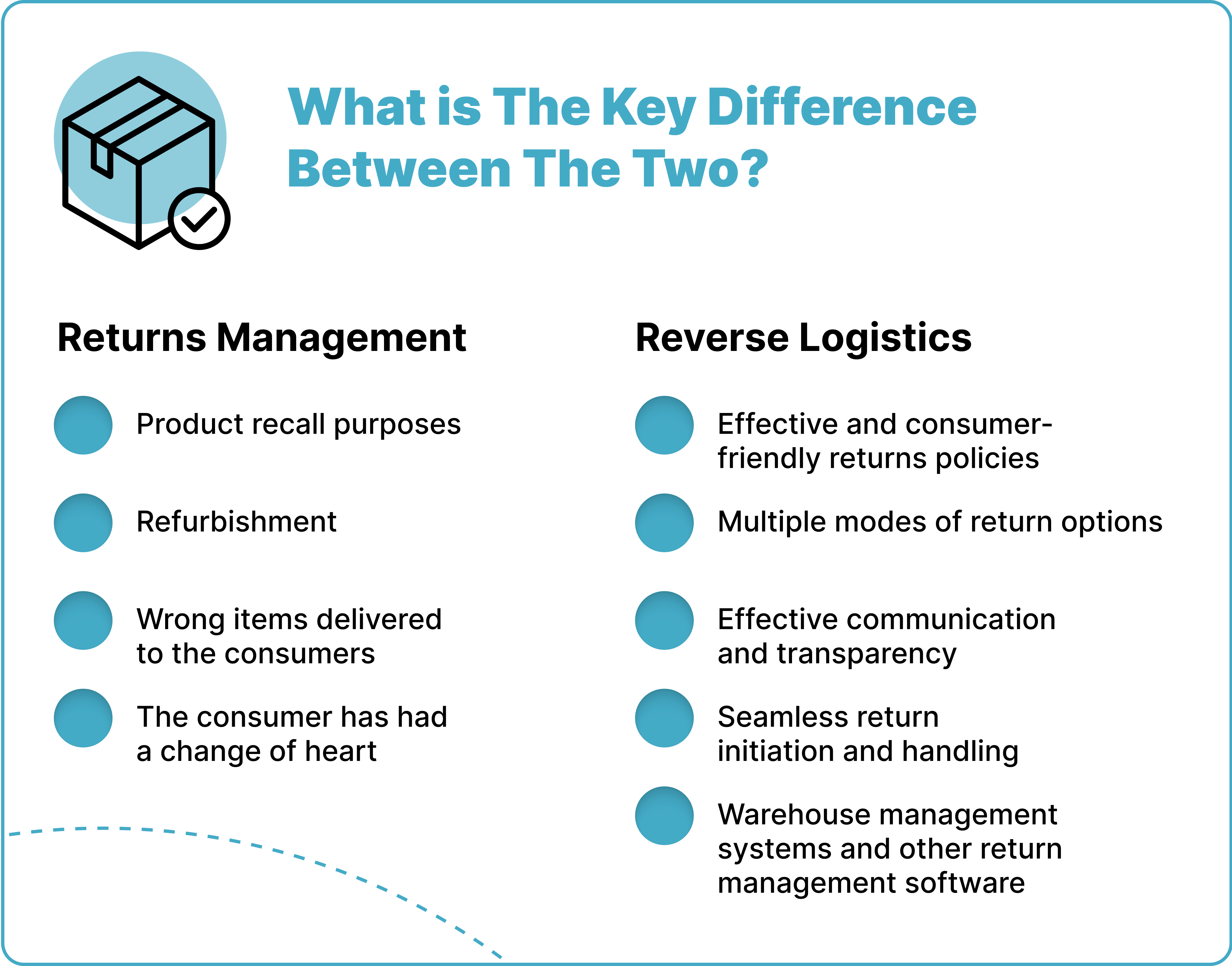
The reverse logistics is the event. It encompasses several activities that allow businesses and supply chains to collect goods of all kinds from consumers. It could be because of
- Product recall purposes
- Refurbishment
- Wrong items delivered to the consumers
- The consumer has had a change of heart
While the reverse logistics process was here before the e-commerce boom and could be traced back to simpler times, the rise of e-commerce certainly resulted in a boom for the industry and forced businesses to take it seriously.
On the other hand, there is no returns management without reverse logistics, but reverse logistics would be a complete mess without it. It is customer-centric and focuses on managing customer expectations and ensuring they have a great experience with the reverse logistics process. It leverages the following to ensure proper handling of the reverse logistics process.
- Effective and consumer-friendly returns policies
- Multiple modes of return options
- Effective communication and transparency
- Seamless return initiation and handling
- Warehouse management systems and other return management software
Think about it this way. Reverse logistics may exist without returns management. But it will not come close to the trillion-dollar behemoth it is today. It will be a messy version.
ReverseLogix is The Key To Effective Reverse Logistics and Returns Management Process
Understanding the difference between the two product return concepts optimizes the entire return process. But like every other part of the modern supply chain and logistics management, it won’t be complete without applying a technology solution. And we have the best solution here at ReverseLogix.
We have solved the problem of complex returns by developing a system that caters to the nuances of product returns. Our solution allows for the automation of the return process, fraud prevention throughout the return process, analytics and tracking, sustainability, and recommerce.
In a world where reverse logistics management is increasingly complicated, you need a solution to “de-complicate and de-construct” the entire operation. Get a demo or view our pricing plans today.
Frequently Asked Questions
The reverse logistics is set up to ensure that consumers have an avenue to return unwanted goods to the supply chain. This way, supply chains can enhance customer satisfaction while also allowing the business and supply chain to use or dispose of these goods in any number of ways.
Returns management helps ensure that the entire return process is properly handled. It is set up to be customer-centric. This way, the business and supply chain is sure that the customers have a seamless experience when returning goods.
It also helps inform the customers of what type of returns are permitted and clarifies the refunding process and options. This may also include the option of store credit and other rewards for an online store.
Reverse logistics and returns management are not without challenges. This includes handling a high volume of returns, complicated return requests process, fraudulent returns, proper inventory management of the returned goods and integrating them back into the system, slow processing due to the volume of returns, and addressing customer inquiries effectively.
However, challenges like this are where an application like ReverseLogix shines best.
To measure the success of reverse logistics and return management process, businesses must effectively track key performance indicators such as:
– return rates
– return processing time
– recovery value
– customer satisfaction
– sustainability and profitability impact
This way, they understand the success and failure of the reverse logistics and return management process.