11 Reasons to Automate Your Reverse Logistics Process
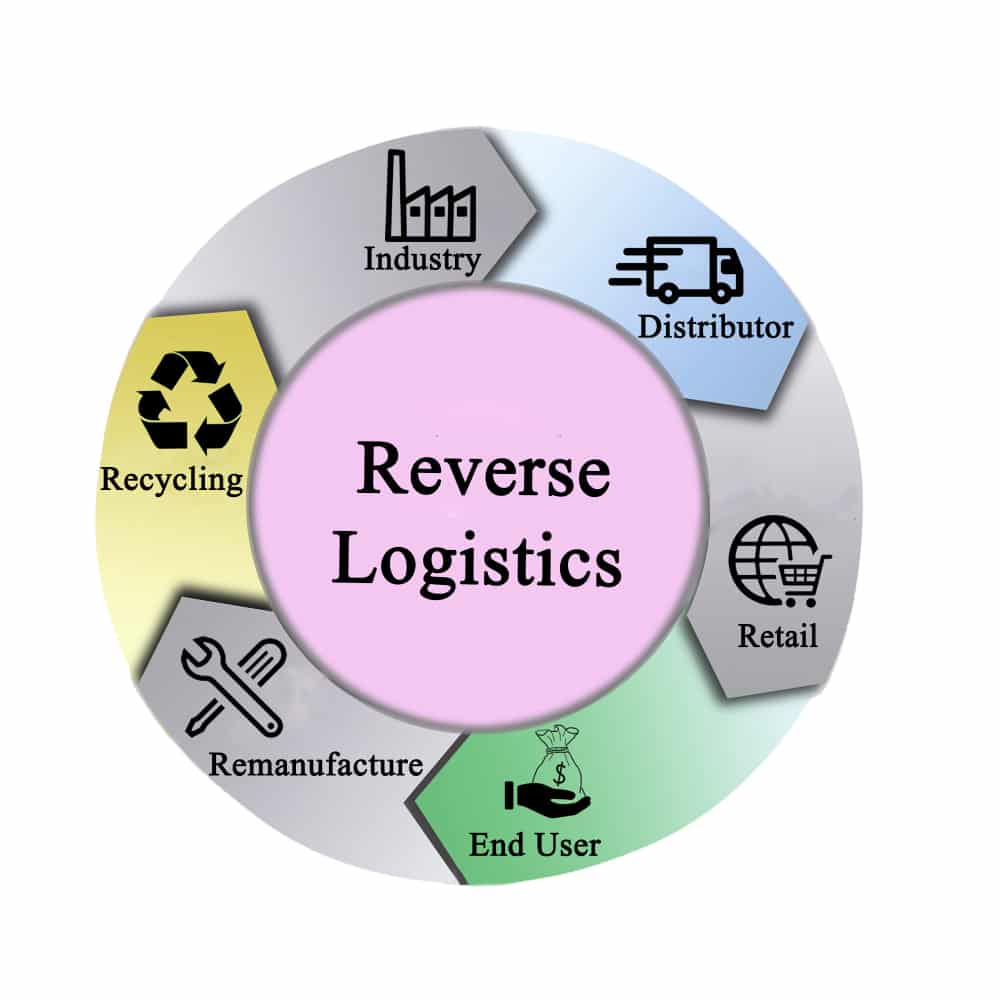
Managing customer returns is harder than ever as online shopping grows. Many smaller businesses handle returns by hand. This process can lead to slow processing, high costs, and unhappy customers, but, using a returns management system to automate your process can help resolve these issues
Automating the returns process speeds it up and reduces mistakes, ultimately improving the customer experience. It also helps companies see patterns, like common return reasons or fraud attempts, which are much harder to catch with manual methods. Plus, automation lets businesses handle returns in a way that saves time and money.
This post will cover the top reasons for automating reverse logistics. From improving inventory management to boosting resale value, automation simplifies returns for everyone.
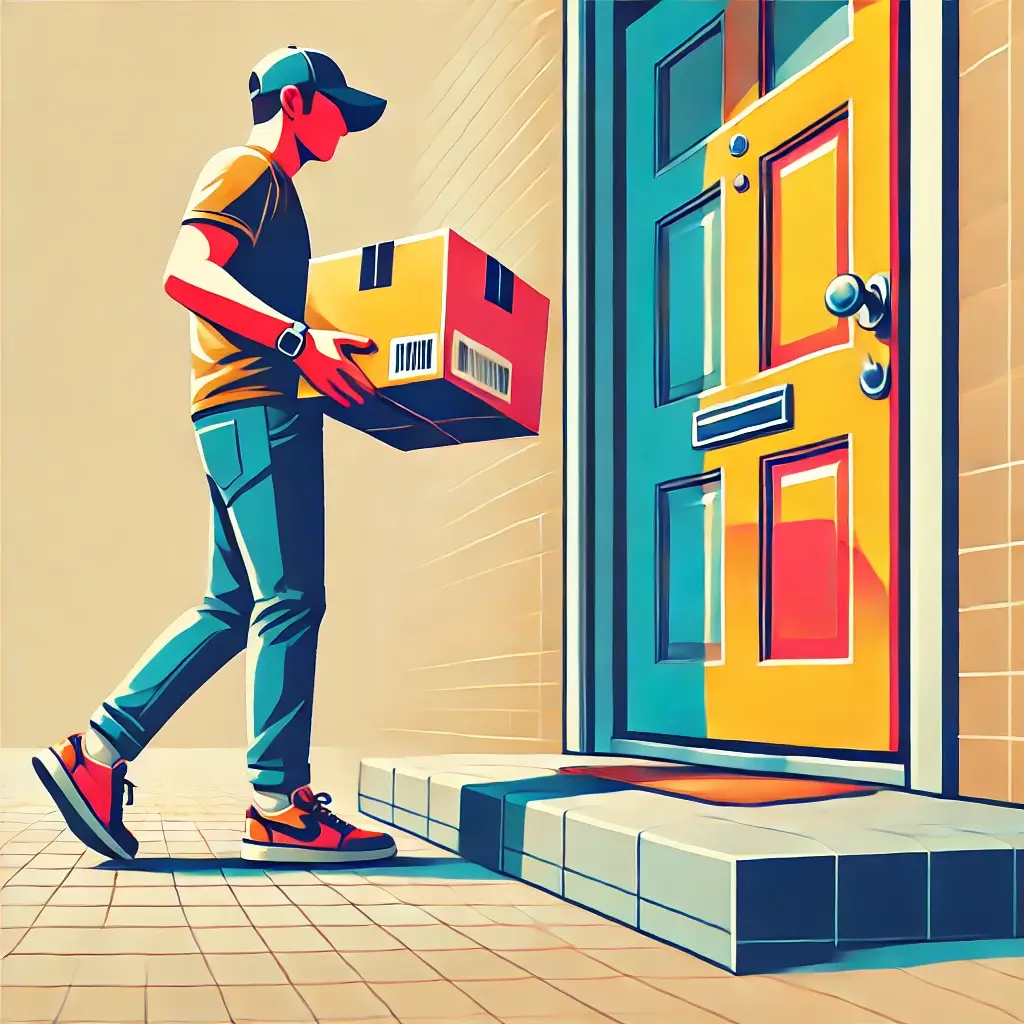
Improved Business Intelligence
Automating reverse logistics doesn’t just speed up returns. It also gives companies valuable data to make smarter business decisions. With returns automation, businesses can collect data on why items are returned, how often, and even where the most returns happen. This data shows patterns that help companies make smart decisions. They can improve their products, spot quality issues, and identify ways to prevent returns.
For example, if a certain product is returned frequently for the same reason, it might signal a design flaw that needs fixing. Understanding these trends helps businesses improve their products or descriptions to reduce returns. Automated systems can track this information in real-time, allowing teams to respond faster.
Better data leads to stronger planning, too. With insights from reverse logistics solutions, companies can predict future return trends. They can also manage inventory more effectively, saving time and resources in the long run.
Heightened Visibility Into Your Returns Process
Automating reverse logistics makes tracking each step in the returns process easier. With manual tracking, returns can get delayed or lost, leading to higher costs and unhappy customers. But returns automation gives teams full visibility into each item, from when it’s shipped back until it’s processed.
This visibility helps businesses catch delays and fix issues right away. For example, if returns pile up in one location, managers can take action to clear the backlog. Real-time tracking also means customers can see where their return is and know when to expect their refund or replacement.
Better visibility speeds up the returns process and reduces mistakes. With fewer errors, customers have a smoother, more reliable return experience, which builds trust and loyalty.
Automated Returns Policy Enforcement & Returns Fraud Detection
Automating your return policy enforcement helps companies stay consistent while reducing costly mistakes. With manual processes, enforcing return rules—like time limits or condition requirements—can be hard to track. Returns automation automatically checks each return against the policy. Doing so ensures only eligible items go through.
Automation also makes it easier to spot return fraud. Fraud can happen when customers return used items as new, claim fake damages, or exploit generous policies. Automated systems can track suspicious patterns. For example, it can flag frequent returns from certain customers or high-value items that are returned often. By highlighting these cases, companies can act quickly to protect their bottom line.
These tools save money and prevent unnecessary losses. The system automatically checks returns for compliance and detects possible fraud. With this handled, businesses can focus on legitimate returns while avoiding costly scams.
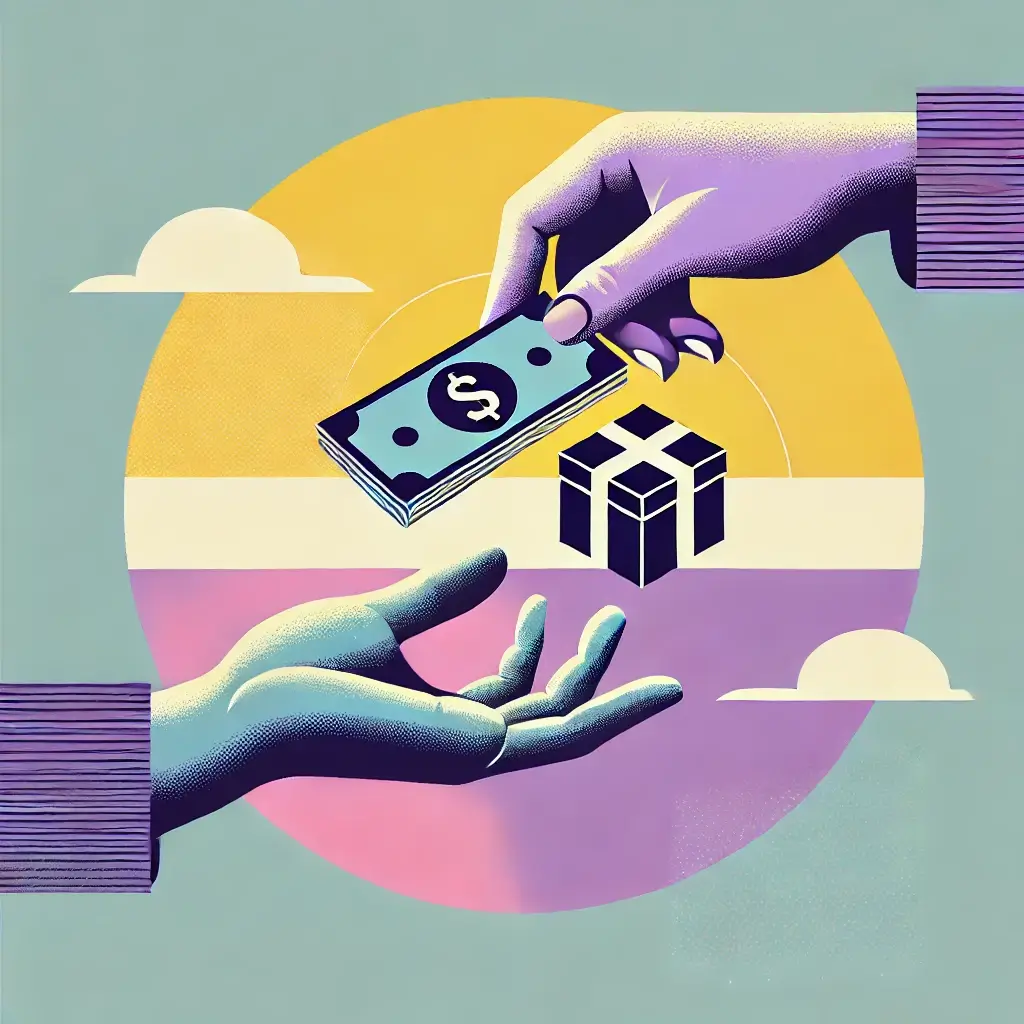
Faster Processing for More Efficiency
Automating reverse logistics speeds up returns with greater efficiency and lower costs. Manual returns handling can be slow and tedious. It involves steps like checking product condition, restocking, and processing refunds. Returns automation makes these steps happen faster and more accurately. Each item is scanned and processed through an automated system, reducing the need for manual work and minimizing delays.
This boost in efficiency means products get back into stock sooner, which is especially helpful for items in high demand. Faster processing also frees up warehouse space and reduces labor expenses, as fewer workers are needed to manage returns. Plus, with automated tracking, customers receive updates on their returns in real-time. This data sharing can lead to a better overall experience.
Fewer Human Errors
Automating the returns process helps reduce mistakes that often happen with manual work. When people handle returns by hand, errors like typing the wrong numbers or losing track of items can slow things down and lead to extra costs. Returns automation lowers these risks by using digital tracking and automatic checks to ensure each step is correct.
Automated systems scan return labels, check item details, and consistently apply return policies. These steps prevent common mix-ups, like refunding the wrong customer or missing important checks on items. With fewer errors, the returns process runs smoothly and costs less.
Reducing mistakes also improves customers’ experiences. Automation makes returns faster and more reliable, ensuring that customers get the right refunds or replacements without delays.
Create a Positive Customer Experience
Automating returns helps create a better customer experience. It makes returns quick, easy, and reliable. Customers who know they can return items without difficulty and get a fast refund or replacement feel more confident shopping with a brand. Returns automation makes this possible by speeding up the process and giving clear updates.
With automated returns, customers can track every step, from returning the item to receiving their refund. This tracking makes the process less stressful since they know what’s happening and when to expect their money back. Faster processing also means customers don’t have to wait as long, which adds to a smooth experience.
Automation also helps by applying return rules the same way for everyone, which reduces mistakes. Fewer errors mean fewer unhappy customers. Ultimately, a simple, quick returns process shows customers that the company cares, which keeps them coming back.
Utilize Auto-Routing to Your Benefit
Automating reverse logistics with an auto-route feature can make returns faster and easier to manage. When a return is sent back, auto-routing decides the best next steps based on set rules. For example, if an item is in good condition, the system may route it directly to restocking. If it needs repair, it might be sent to a service center. This automated decision-making saves time and reduces manual sorting.
Auto-routing helps businesses reduce storage and handling costs. By automatically directing items, companies can avoid holding products too long. This speeds up processing, frees up space, and returns products to stock faster.
The auto-route feature also improves the customer experience by reducing delays. A clear, efficient system ensures customers get their refunds or replacements sooner. Auto-routing is a powerful tool that makes the returns process quicker and more efficient.
Simplify the Returns Merchandise Authorization Process
Automating the Returns Merchandise Authorization (RMA) process makes returns smoother and faster. An RMA is the approval a customer needs to send back an item, and it often includes information like the reason for the return and the item’s condition. When handled manually, this process can be slow and unclear, leading to frustration and delays for customers and staff.
With returns automation, the return merchandise authorization becomes quick and easy. Customers can request an RMA online, and the system can instantly check if the item qualifies for return based on set policies. Approved returns get processed immediately, while items that don’t qualify are flagged, saving time and effort.
Automating RMAs speeds up the return and improves accuracy by reducing human error. A simple, streamlined RMA process helps customers feel supported and confident. It encourages them to shop with the brand again.
Easier Warranty & Repairs Management
Warranties can be tricky. However, automating warranty and repair management makes handling returns for product issues easier. When a customer sends back an item for repair or because of a warranty claim, a manual process can lead to delays, confusion, and mistakes. With returns automation, companies can quickly track warranty coverage. They can also check repair needs and efficiently route items to the right place.
Automated systems can instantly verify if an item is under warranty and create a clear repair path. For example, if a product qualifies, it may be automatically sent to the repair management team or a service center. This speeds up the process, so customers don’t have to wait long for repaired or replaced items.
A well-oiled, automated warranty and repair process improves customer satisfaction. Reducing wait times and keeping customers informed builds trust and simplifies returns.
Maximize Resale Value of Products to Increase ROI
Automating reverse logistics can help companies get the most value from returned items. A good system quickly processes returns for resale, also known as recommerce. When returns are handled manually, products often sit in storage, losing value over time. Returns automation speeds up the process. It can quickly ensure items are evaluated, repaired, and returned to stock or prepared for resale.
Fast processing also improves inventory turnover, which means items move in and out of stock quickly. This helps companies avoid overstock and keeps warehouses organized. With automated sorting and tracking, returned items can be sorted based on condition. Businesses can then decide if they’ll be resold, discounted, or recycled.
Using recommerce strategies and automated processes, companies can recover more value from returns. Overall, this can increase their return on investment (ROI). The approach makes better use of returned products, reduces waste, and contributes to higher profits.
Improved Inventory Management
Automating reverse logistics leads to better inventory management. It streamlines how returned items are processed, sorted, and restocked. When companies handle returns manually, they risk delays and inaccurate counts, which can lead to overstock or stockouts. With returns automation, every item is scanned and tracked in real-time, so inventory levels stay accurate and up-to-date.
Automated systems help companies know what’s in stock and what’s being returned. This real-time information allows for smarter decisions about restocking or redistributing items. It helps brands reduce excess inventory and free up valuable warehouse space. It also means faster turnaround for items in demand to be restocked and resold sooner.
Better inventory management also leads to lower storage costs and less waste, as items spend less time sitting unused. Automation helps keep the entire supply chain running smoothly. It ensures products flow efficiently from return to resale, all while meeting customer needs.
Why Automating Reverse Logistics is Key to Business Success
Automating reverse logistics improves the customer experience. It also speeds up returns and helps businesses save money. With returns automation, companies reduce mistakes, boost processing speed, and gain valuable insights. This streamlined approach allows businesses to handle returns more efficiently. It also helps keep customers happy with faster refunds and replacements.
Ready to see how automation can optimize your returns process? Discover how ReverseLogix can help your business easily handle returns. Request a demo today to experience the benefits of a fully integrated reverse logistics solution.