The Reverse Logistics Economics: Cost-Benefit Analysis for Retail Businesses
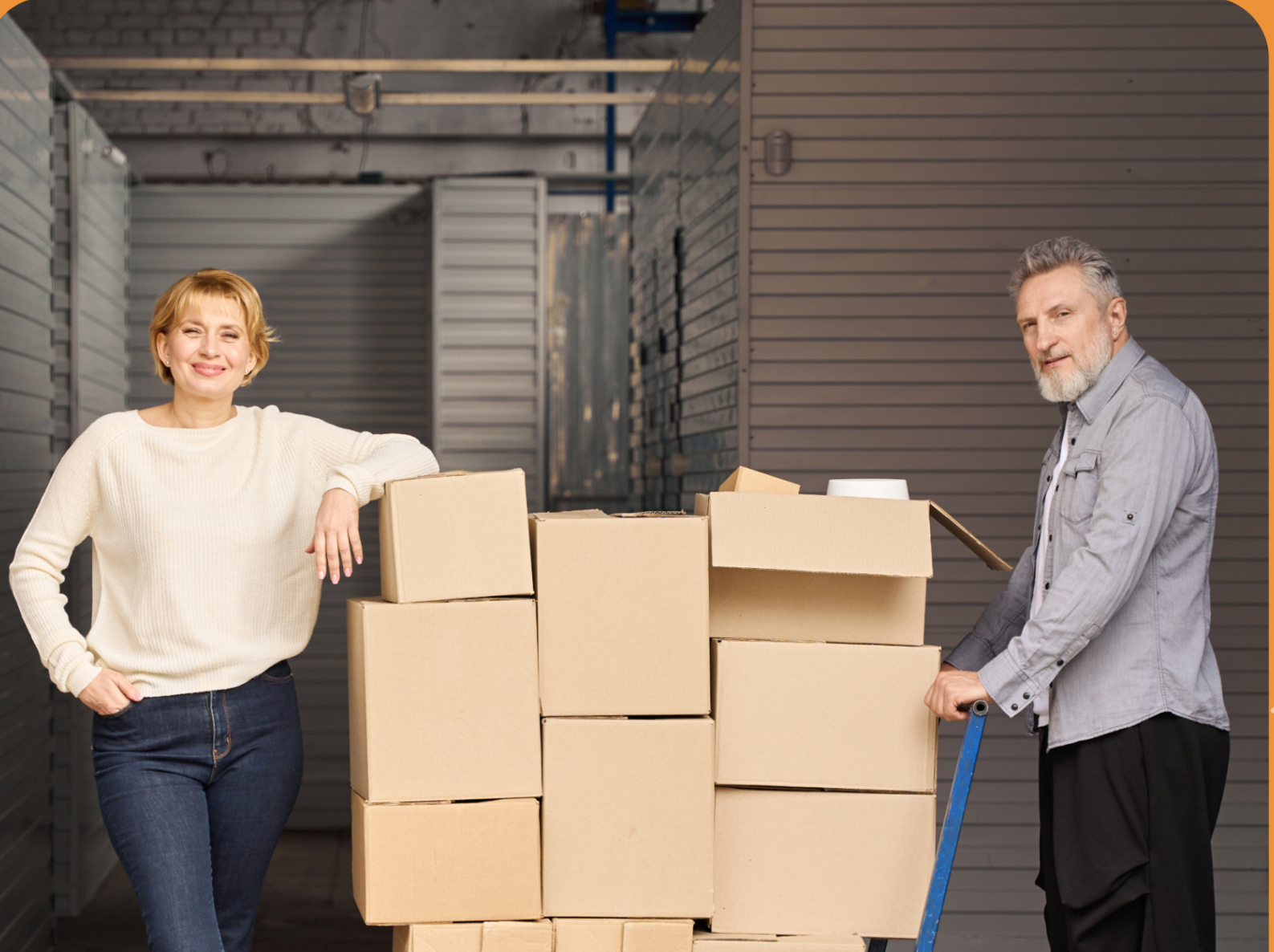
Since the turn of the century, the growth in operations, size, and number of e-commerce platforms has seen relative growth in managing and processing customer product returns. However, to manage these returns effectively, your company must rely extensively on reverse logistics, which ensures your customers are satisfied with the e-commerce platform’s or online retailer’s services.
The idea of reverse logistics is to ensure profitability in return management. It returns products from customers to the e-commerce supply chain but goes beyond that. Reverse logistics ensures that the goods are returned in good condition, sent to the correct warehouses, properly integrated with inventory management, or disposed of, if necessary. However, you will quickly find that it is not always as straightforward as that.
Yes, reverse logistics is necessary in today’s retail operations, especially those online, but implementing it successfully comes with its fair share of challenges and opportunities. Understanding these and then balancing them will determine how successful the returns management process gets. This article will help to unveil and understand the economics of reverse logistics.
Understanding The Tangible and Intangible Cost(s) Implications of Reverse Logistics
The nature of online retail is such that customers cannot see what they are actually purchasing. This means there is a level of blind trust. To build that trust, e-commerce companies and platforms had to promise to take returns if necessary via the reverse logistics process.
But what are the direct and indirect costs of reverse logistics for these companies?
1. Transportation Costs
When moving returned goods, you must consider two major transport expenses: inbound expenses, which involve shipments from customers to return centers, and outbound expenses, which encompass all expenses associated with transporting products from return centers to warehouses, repair facilities, or disposal sites.
The problem with these expenses is that the products are kept on the move longer than intended, exposing them to various risks. Then, there is the challenge of one poorly optimized process inflating these expenses. These problems emphasize the need for robust route planning and third-party logistics provider selection.
2. Handling Costs
For product returns to be effective, they must undergo various steps and processes, including receiving and inspecting items, sorting, grading, and labeling. All of these require handling, which results in more infrastructural costs.
Some of these products may also require repackaging before they are resold or disposed of, further adding to the costs of the process. Managing all of these effectively will require robust and well-thought-out inventory management because it will allow your team to track returned goods and determine the best course of action.
3. Labor and Technology Costs
As much as there is a push to replace labor with technology, the most efficient logistics and supply chain operations have balanced the two. On one hand, a dedicated workforce is needed to process returns efficiently. These employees inspect, sort, and restock returned goods and manage the overall returns process. However, labor costs can escalate if there is a lack of streamlined procedures or too much reliance on traditional or manual methods of returns processing.
On the other hand, they cannot do them without adequate investment in technology solutions such as returns management systems and warehouse automation. These tech solutions are expensive, but they are necessary to improve efficiency by reducing errors, automating workflows, and integrating with existing supply chain systems to minimize disruptions.
4. Disposal Costs
Some products cannot be resold and must be disposed of, which increases business expenses. Disposal fees vary based on product type and regulations, and improper handling can lead to additional penalties or reputational damage.
5. Customer Service Costs
Today, customers want transparency, which is fair, but that may also mean additional expenses for your business. There is the option of manually handling customer inquiries and resolutions, but that can lead to delays, which is also expensive as you may lose that customer. The other option is to use solutions like this to improve the customer’s overall experience
Economic Benefits of Effective Reverse Logistics
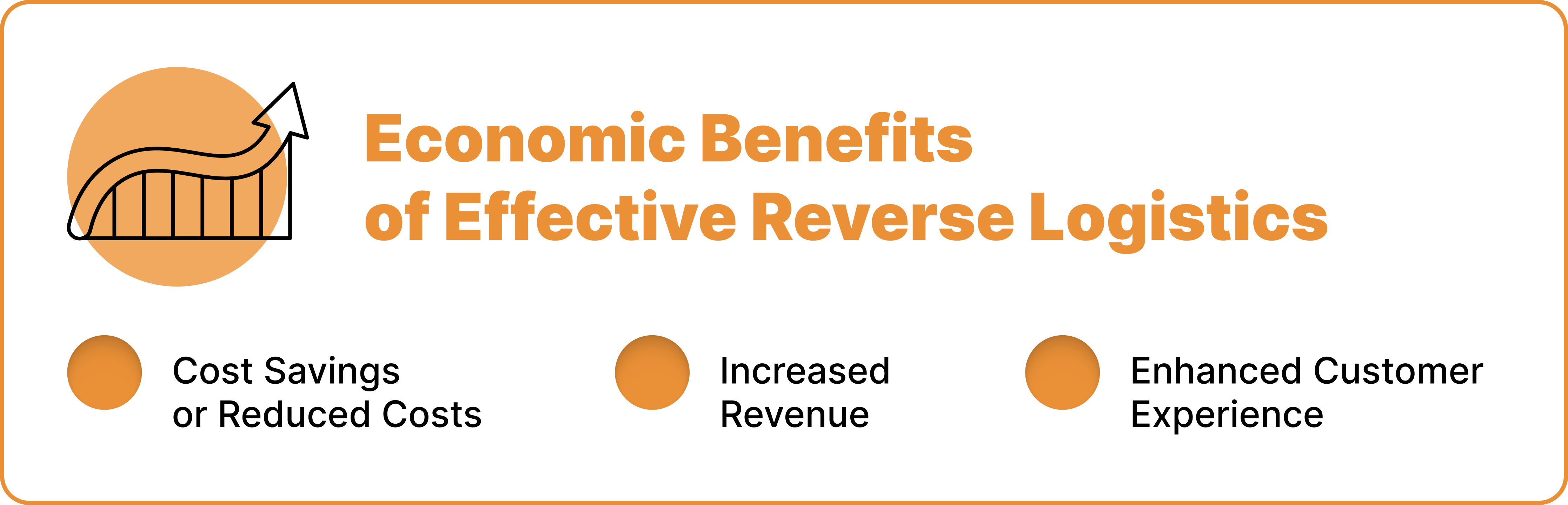
Although many challenges and cost implications complicate the reverse logistics operation, it is not without its benefits. In this section, we will review some of its economic benefits and explain how to ensure that it works for you.
1. Cost Savings or Reduced Costs
Suppose you partner with the right carrier that is also cost-effective and optimizes transportation routes. In that case, reverse logistics can reduce the process’s overall cost and minimize the supply chain’s expenses. However, it is not all up to the carrier. Your ability to streamline the handling processes reduces labor costs, while investing in technology leads to faster processing times, keeping customers happy.
Optimizing the reverse logistics process also requires taking adequate steps to prevent unnecessary returns, such as improving product quality and providing accurate descriptions that limit costs. Refurbishing and reselling returned items can further lower disposal costs.
2. Increased Revenue
A well-run reverse logistics operation can increase revenue for second-hand or recommerce products, especially when these goods meet quality standards and can be resold through various channels, including online marketplaces and outlet stores. Materials from unsellable items can be salvaged or recycled, turning waste into revenue. A seamless return experience fosters customer trust, increasing repeat purchases.
3. Enhanced Customer Experience
Your customers are understandably nervous about the returns process. Now, imagine offering them a transparent and hassle-free return process. That move will foster customer trust and repeat purchases or encourage customer loyalty. The trick is to guarantee quick refunds and replacements. A well-managed reverse logistics system reassures customers they can shop confidently, improving overall customer satisfaction.
Cost-Benefit Analysis Framework
Understanding the cost-benefit analysis of the reverse logistics process can help you decide whether or not it is still worth investing in today’s dynamic economy.
1. Identify and Quantify Costs
Businesses need a detailed model to track and analyze reverse logistics expenses. Understanding the true cost of handling returns enables better decision-making and budgeting.
2. Measure and Track Key Performance Indicators (KPIs)
Tracking metrics such as return rates, processing times, customer satisfaction, and cost per return helps identify inefficiencies. Consistent monitoring ensures that operations remain aligned with financial goals.
3. Conduct a Return on Investment (ROI) Analysis
Evaluating the financial return of various reverse logistics strategies can help businesses determine where to allocate resources. Comparing projected costs against expected benefits highlights areas for improvement and investment.
4. Regularly Review and Adjust
Ongoing analysis ensures that processes remain efficient. Businesses should periodically reassess their reverse logistics approach to incorporate new technologies and optimize workflows.
Enhance Your Reverse Logistics Workflows With ReverseLogix
Implementing a resilient reverse logistics process requires good information and visibility from start to finish. But to do that, you need efficient returns management and the right reverse logistics software package that guarantees operational efficiency.
And that is why ReverseLogix is vital to your reverse supply chain and logistics needs. With our solutions, you can identify gaps or potential problems in your existing process and work towards streamlining returns, reducing costs, and improving customer satisfaction. Find out how the ReverseLogix platform can help you with this process. Get a Demo today.
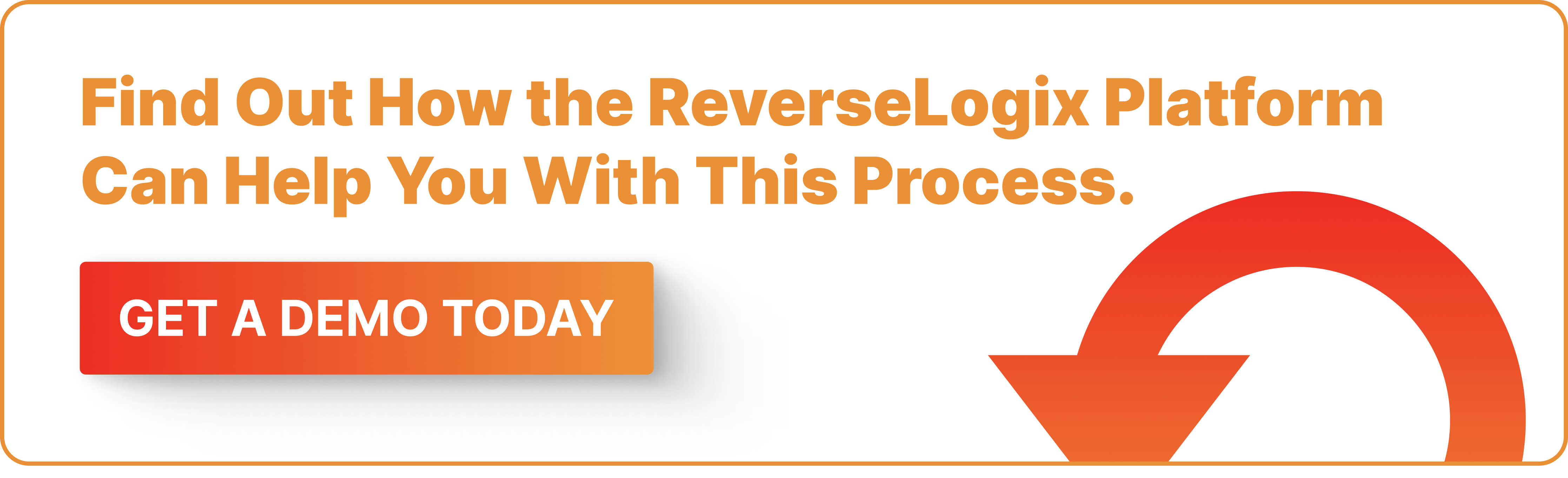
Frequently Asked Questions
Hidden costs of reverse logistics include high transportation, labor, and inventory expenses. Restocking inefficiencies, customer service demands, and disposal fees add to costs. Fraud, technology investments, and legal compliance increase financial strain. Poor return management can also harm brand reputation.
Check their experience with businesses similar to yours. Look for case studies, client testimonials, or certifications indicating their expertise in handling your product type, whether it’s electronics, apparel, or perishables.
Track return rates, processing time, and transportation expenses to assess future reverse logistics costs. Analyze labor, inventory, and disposal costs while considering fraud risks. Use predictive analytics, automation, and sustainability measures to improve efficiency. Review financial data regularly and adjust strategies to control expenses.