Analyzing The Cost Benefit of Outsourcing Reverse Logistics Operations
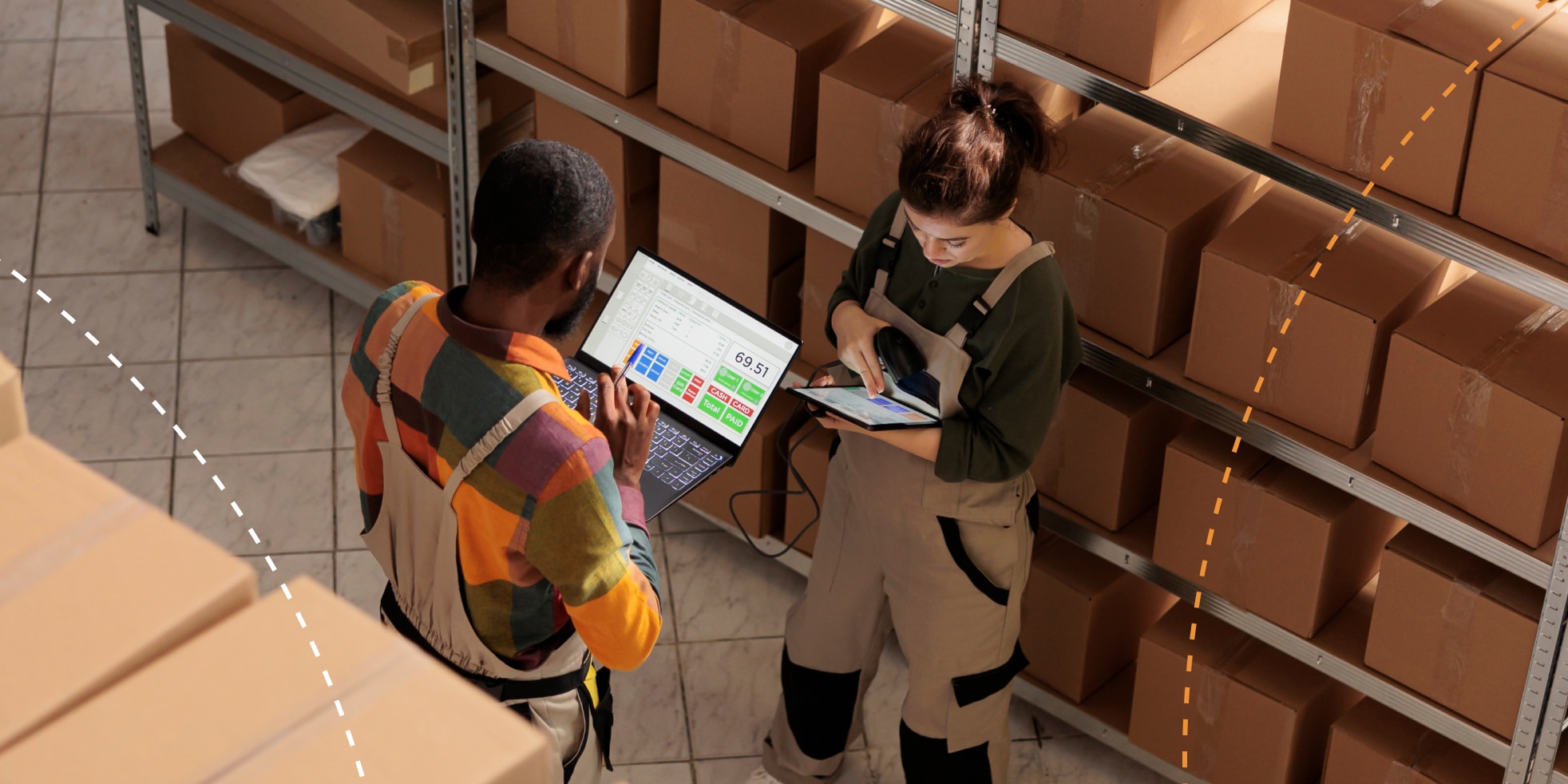
Outsourcing the reverse logistics processhttps://www.reverselogix.com/industry-updates/logistics-vs-supply-chain-management/ offers a range of potential benefits to a business or supply chain by transferring the management of returns to an external provider. The cost benefits from outsourcing could be financial, operational, or both. Carefully analyzing the benefits and downsides will go a long way to help you make the right decision.
The quality of the reverse logistics process is critical in today’s supply chain landscape. It can be a very cumbersome and problematic process though. Especially when the business or supply chain does not have the necessary resources and expertise to optimize the operation. In the past, it was typical for businesses struggling with reverse logistics to shut down an operation because they could not make it work.
However, that is not an option because of how critical the reverse logistics process is to businesses and supply chains today. They must make it work, and this is where outsourcing comes into play. With outsourcing, these businesses have a way out to avoid the burden of managing reverse logistics operations in-house, while leveraging it to boost customer experience.
What is Outsourcing?
Outsourcing is simply transferring parts or processes of the supply chain to better-qualified people and businesses. You can do this for several parts of the supply chain. Some companies outsource their entire supply chain or large parts of it. It could be any part of the supply chain, from inventory management to fulfillment, manufacturing, or logistics processes.
The entire point of the outsourcing strategy is to have companies leverage expertise and experience, as well as reduce costs of operations and simplify them. In 2020, more than 42% of businesses outsourced their logistics operations, with the numbers only set to rise.
Cost Benefit of Outsourcing The Reverse Logistics Process
Outsourcing any part of logistics management, particularly reverse logistics, can be a major decision. And with good reason, considering it deals directly with the end customers. There are many reasons for and against it. However, as a company or a retailer, these reasons may impact the business differently. The principles are the same, though.
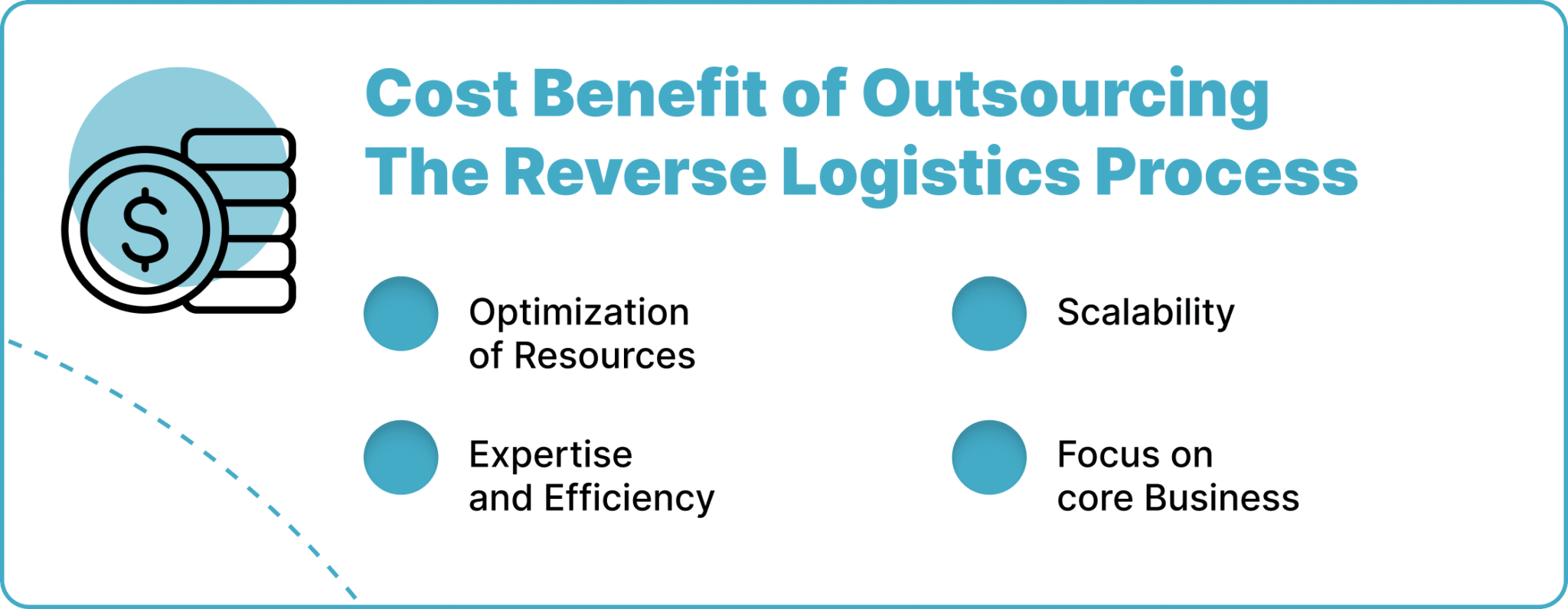
Optimization of Resources
Resources (including people, infrastructures, and other tools) can be expensive to maintain. They are especially problematic when the supply chain is not properly utilizing them. For instance, underutilized infrastructure can cause all sorts of problems for the business, especially from a financial standpoint. The same applies to people.
Having all these and failing to optimize does not benefit the reverse logistics process or the supply chain. However, by outsourcing reverse logistics, you can leverage the resources of the third-party provider you are outsourcing to, making the entire operation cheaper and more streamlined for success. In a competitive business environment, it allows your business to stand out and do more with its resources, creating a better reverse logistics operation.
Expertise and Efficiency
Typically, the business you are outsourcing to has the expertise, infrastructure, and experience to make your reverse logistics as smooth as possible. They also work with other businesses and have more efficient processes or systems to make the reverse logistics process seamless.
You can have all that at your disposal without paying much for control and optimization. They take all the risks, and you enjoy most of the rewards. Because of them, you can strengthen your overall logistics and supply chain process to be more efficient.
Scalability
Scaling operations can be expensive any way you look at it. Imagine scaling up. The cost of infrastructure alone can be overwhelming. This will typically include creating more warehouse space and purchasing more vehicles. If your supply chain has all of these, now imagine scaling down. The waste and termination fees could be enough to disrupt a small supply chain.
However, with outsourcing, you can achieve scalability in your returns management without directly investing in the process. You can scale down operations or scale up without additional cost to your supply chain. Again, it is a situation where the third-party reverse logistics business takes all the risks. And your supply chain reaps the rewards.
Focus on Core Business
As a business, you will have several moving parts and operations but one core competency. Handling the nitty gritty of all these parts and processes could distract from the business’s primary purpose. For instance, a fashion business struggling to integrate reverse logistics operations and make it as seamless as possible could be diverting attention from the company’s core function.
Ultimately, this distraction can begin impacting productivity, profitability, and the ability to focus on enhancing the customer’s experience. This is the primary reason major businesses and brands outsource their reverse logistics process and other parts of their supply chain management. They want to ensure they can save costs while enhancing the customer’s experience.
Challenge of Outsourcing the Reverse Logistics Process
Although there are numerous tangible benefits to outsourcing the reverse logistics process, there are also potential challenges. These could typically stem from partnering with the wrong partners or failure to integrate properly.
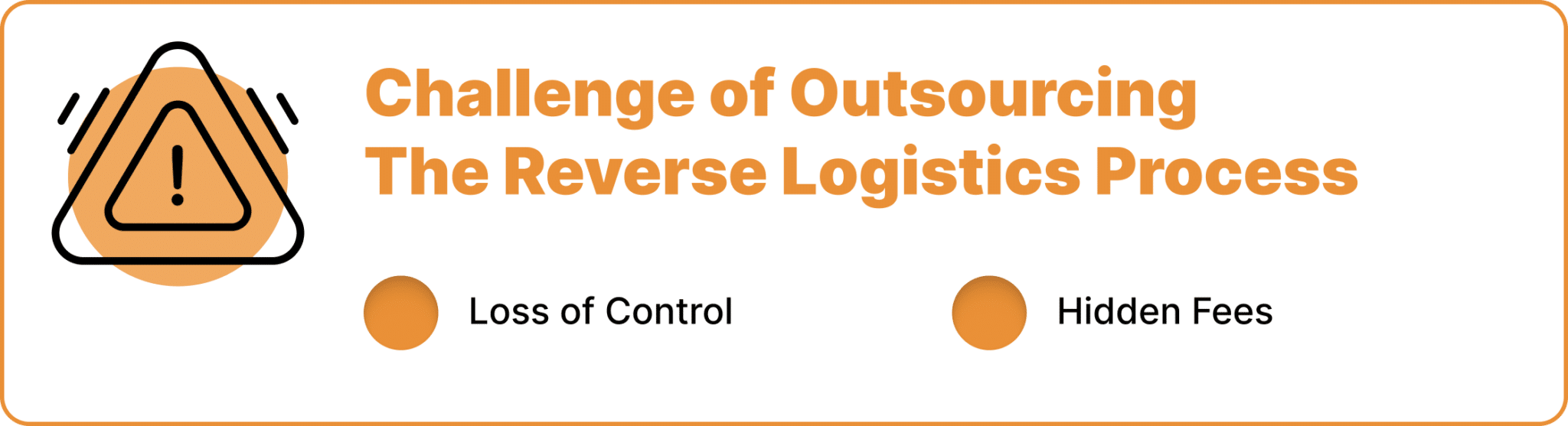
Loss of Control
Reverse logistics outsourcing could cause your supply chain to relinquish some or a lot of control over the return process. This could result in inefficiencies, poor sustainability, and poor customer experience. Typically, the loss of control is caused by a failure to establish expectations and boundaries.
Hidden Fees
The outsourcing contract could often have hidden fees and charges, resulting in more than anticipated expenses. Ultimately, this can impact the profitability of the process and the supply chain. To avoid these, ensure proper negotiations and scrutinization of contracts. The expectations, goals, and fees of outsourcing relationship should be clearly communicated to avoid misunderstanding.
Zero Downside With ReverseLogix
ReverseLogix is the only end-to-end reverse logistics platform that has solved the problem of complex logistics operations. With our platform, you can initiate returns, configure return processing, and even handle repairs. All with ease.
With our solutions, you have all the upsides and none of the downsides. You can streamline and optimize your reverse logistics without worrying about integration problems, loss of control, and hidden fees.
Why? You have a platform that allows you to maintain visibility and control over your operations by connecting the customer-facing service portal with your commerce platform and warehouse operations. Our contracts are clear as day, and there are no hidden charges. View our pricing plans to learn more.
Frequently Asked Questions
Q1: Will outsourcing slow down my reverse logistics process?
It depends on the provider. An experienced provider would have established processes and technology to handle returns, leading to faster processing times and improved customer satisfaction.
Q2: Can an outsourcing partner handle the complexities of different return scenarios?
Unlike your in-house team, reverse logistics partners specialize in various return types, ensuring proper care and disposition for each item, from defective products to customer remorse.
Q3: Will outsourcing reverse logistics processes actually save me money?
The short answer is yes. You can expect cost savings from reduced overhead costs of the supply chain. With outsourcing, you can eliminate warehouse space and labor costs associated with in-house reverse logistics processes. However, outsourcing with the wrong partners can result in nefarious contracts with hidden fees. It is important to be careful during the partnership and negotiation process.
Q4: What are some of the hidden costs I should be aware of in outsourcing contracts?
Some hidden charges you should look out for are outsourcing costs that the providers will charge. Some of them are processing charges, per-item handling fees, and penalties for exceeding return volumes.