Why Your Yard Management Team Needs Better Software
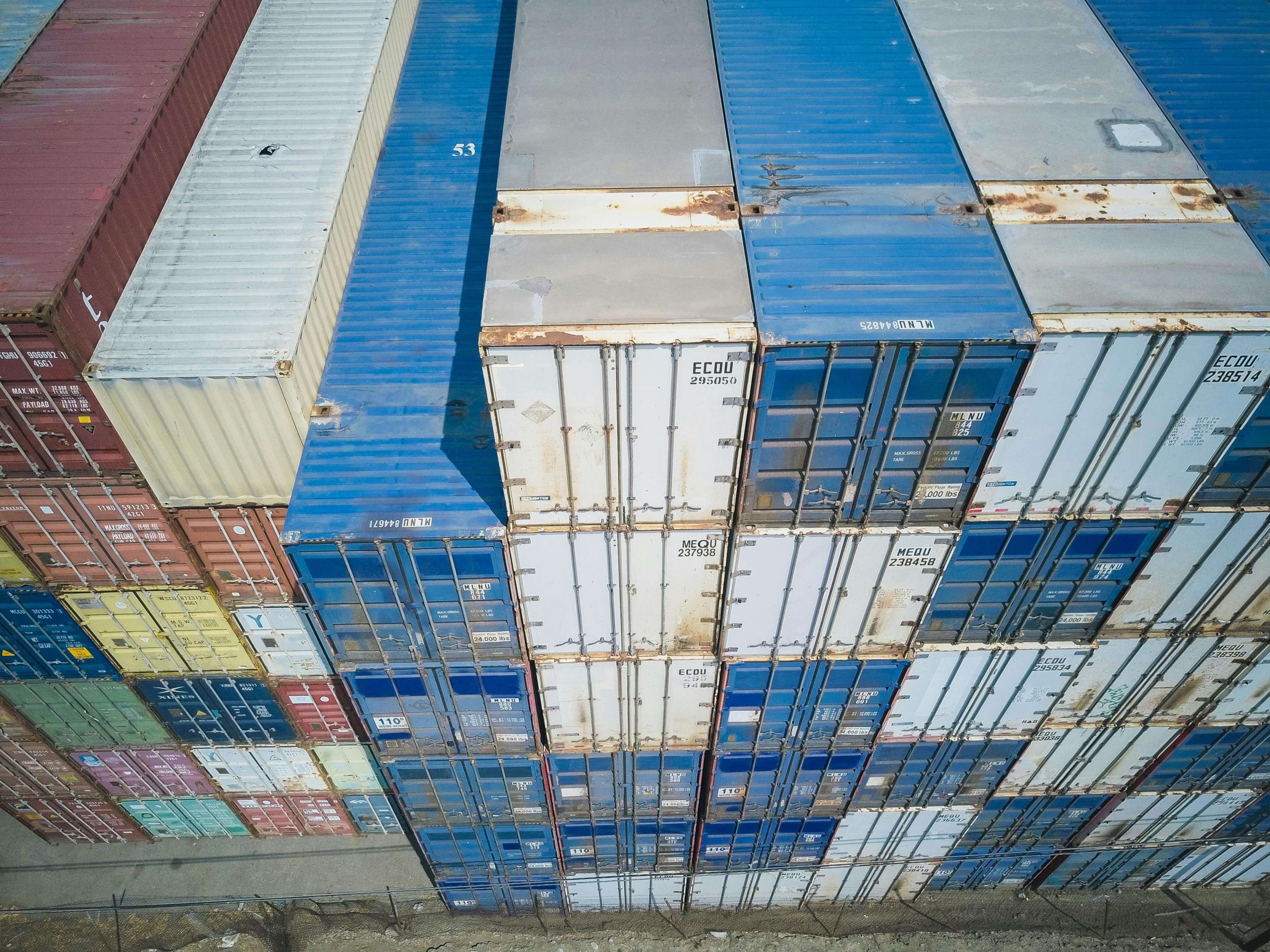
Yard management is the bridge between warehouse functions and transportation. Seamless communication benefits the entire supply chain. If you’re still using manual tools like clipboards and spreadsheets, you’re likely dealing with lost time, lost trailers, and miscommunication. Slowdowns like these cost you money and can make your partners unhappy.
Implementing modern yard management can quickly eliminate these issues. It gives teams real-time visibility and automates routine tasks. The result? A more efficient, connected, and strategic yard.
What is Yard Management
Yard management involves coordinating trailers, containers, trucks, and other assets in a facility’s yard. It ensures the right vehicles and goods move in and out at the right time.
This function bridges warehouse activities and transportation. A well-run yard has clear docks and drivers on schedule so inventory never stops flowing.
Effective yard management means faster turnaround times. It can also lower labor and detention costs and improve handoffs across the supply chain.
What is the difference between a yard and a warehouse? The yard handles the movement and staging of trucks and containers. The warehouse manages storage, picking, and inventory control inside the building. |
What is Yard Management Software?
Yard Management Software (YMS) automates and streamlines a yard’s daily procedures. Teams can manage vehicles, trailers, and shipments without relying on paper or spreadsheets.
The core features that make this possible are real-time asset tracking, digital yard maps, and automated appointment scheduling. YMS often integrates with warehouse and transportation systems for better coordination.
What are the three components of yard management? The three main components are yard visibility, task management, and gate control. Together, they ensure efficient flow and control of assets in and out of the yard. |
Core Challenges Yard Management Teams Face
Yard management becomes a daily struggle when you’re not prepared. Manual tasks, rising costs, and poor communication slow everything down and reduce yard productivity.
Inefficient Manual Processes
Many yard teams still rely on outdated tools like radios, clipboards, and spreadsheets. They manually log trailer locations, schedule gate times, and relay updates across teams.
These tasks slow everything down and are prone to error. A trailer might be misplaced. A driver could miss their window. A spreadsheet might not reflect the latest yard status.
When errors stack up, essential functions fall behind schedule. Setbacks ripple through the supply chain, pushing costs and frustrating customers who expect faster, more accurate deliveries.
Operating Expenses
Gate delays, detention fees, and wasted fuel from idling trucks all add up. Tracking issues and slow communication waste labor and equipment. These inefficiencies lead to longer dwell times and poor use of space and resources. Missed dock appointments and disorganized staging increase avoidable expenses.
That’s why you must prioritize controlling these costs to improve profit. The resulting improvement to service levels means you’ll meet delivery promises and keep satisfied partners.
Overtime Labor
Lack of workload insight means labor hours are often tracked manually. This leads to overstaffing during slow periods and scrambling during busy shifts.
The result is excess overtime, which inflates payroll and weakens team morale. Constant overwork can also cause mistakes and burnout.
You can strategize better when you can see ahead. Managers must assign a proper team to the appropriate place to encourage higher productivity while keeping labor costs in check.
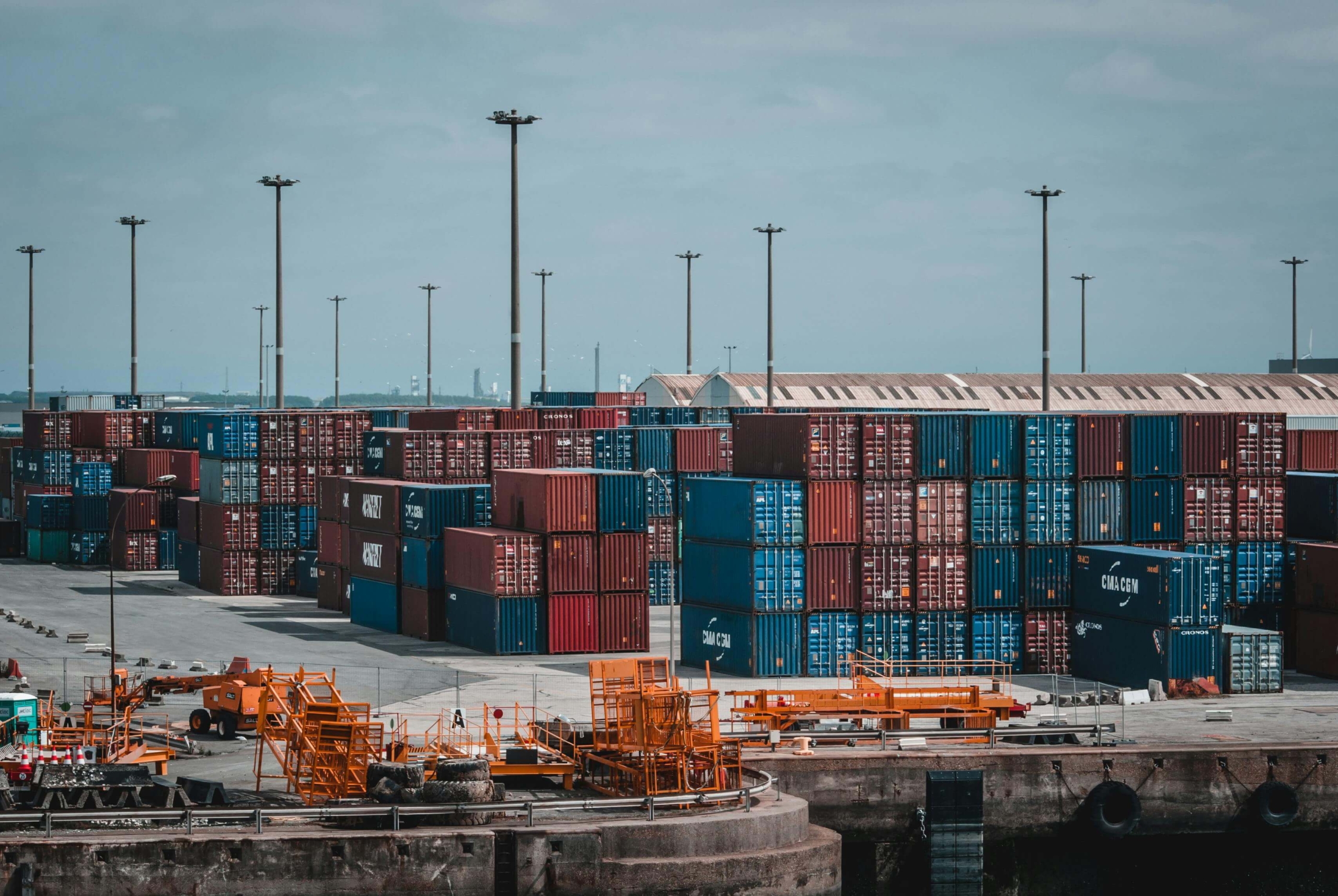
Workflow Bottlenecks & Communication Issues
Things break down fast when yard teams, drivers, and warehouse staff lack communication. Many still rely on radios or phone calls, which can be confusing.
Common issues that result from miscommunication include misrouted trailers, missed dock times, and long driver wait times. Managers lose track of where things must go when they don’t have a clear view of the big picture.
These problems reduce the number of shipments you can move daily, making it harder to stay on schedule. Drivers also get frustrated, which can hurt your reputation and increase turnover. A lack of coordination weakens your whole supply chain.
How Yard Management Software Benefits Your Yard Management Team
A modern yard system acts like a returns management system by streamlining every step from check-in to departure. The following sections show how software improves speed, accuracy, and teamwork across the yard.
Automate the Important Tasks
Yard Management Software takes over time-consuming tasks like trailer check-ins, gate scheduling, and inventory tracking. Handling these manually can be slow and prone to error.
With automation, updates happen in real time. Staff can focus on solving problems and moving shipments faster instead of hunting down paperwork or searching for misplaced trailers.
Better accuracy and faster workflows mean higher output with the same team. The return on investment comes from less downtime, better use of labor, and streamlined yard functions overall.
5 Things a Reverse Logistics Software Platform Must Have Today Learn what features top platforms include. Explore what reverse logistics software should include to stay competitive and efficient. |
Optimize Driver Assessments & Dynamic Tasks
In a busy 3PL yard, timing is everything. Yard Management Software uses real-time data to adjust schedules and update tasks as conditions change.
The system quickly reassigns work according to any shift in plans. This way, drivers are constantly moving instead of waiting for instructions. It also reduces bottlenecks and shortens dwell times.
Dynamic scheduling improves yard flow and ensures flexibility in your daily functions. Drivers stay productive, and the yard stays responsive to daily challenges.
Improve Decision-Making and Visibility
A strong returns management system gives you eyes on every part of the yard. With real-time tracking tools like RFID, barcodes, and GPS, managers can see where trailers are and what’s ready to move.
Exploring Reverse Logistics Platforms: A Look at ReverseLogix’s System Find out how the ReverseLogix platform strengthens logistics. This article reviews the tools that help manage yard operations and returns. |
Digital records make audits easier and help track inventory without missing a thing. You don’t need to dig through paperwork to check trailer status or prove compliance. Even better, it reinforces better decisions about staffing, equipment, and space.
What is yard storage in shipping? Yard storage refers to holding trailers or containers in a facility’s yard before they move to a dock or another location. |
Better Team Coordination & Communication
A 3PL yard runs better when everyone’s on the same page. Yard Management Software connects teams with real-time updates across devices.
With shared dashboards, alerts, and automated status changes, all teams (yard, warehouse, and drivers) see the same information simultaneously. There’s no need to chase down updates or rely on radio calls.
Proper communication sets you up for success, eliminating mistakes, missed assignments, and miscommunication. Strong, effective coordination means solving problems faster and keeping everything on track.
How ReverseLogix Helps Your Yard Management Team
A modern YMS should offer real-time tracking, automation, system integration, and powerful analytics. ReverseLogix delivers all of this in a single, easy-to-use platform.
Our solution helps yard teams move faster, cut costs, and stay in sync, no matter how complicated the operation.
Explore our returns management system to see how it reinforces your logistics flow. Ready for a closer look? Request a demo today.