A third-party logistics (3PL) provider helps businesses manage their supply chain operations. They handle tasks like storing inventory, packing orders, and shipping products to customers. Businesses partner with 3PLs to improve efficiency, reduce costs, and focus on their main goals, including growing sales or creating new products.
When a business works with a 3PL, the process begins with inventory management. The business sends its products to the 3PL’s warehouse, where the 3PL tracks stock levels and keeps items organized. When an order is placed, the 3PL picks, packs, and ships the product. They also coordinate shipping by finding the best carriers and providing tracking information.
Although 3PLs handle many logistics tasks, they are not the only providers in the logistics industry. Businesses may also work with freight forwarders, 2PLs, and even 4PLs. Let’s examine their roles to better understand how 3PLs compare to these other providers.
Freight Forwarding vs. 2PL
Freight forwarders and second-party logistics (2PL) providers focus on transporting goods but work differently. A 2PL provider owns the physical assets used for transportation, such as trucks, ships, or airplanes. For example, a trucking company that delivers goods from a warehouse to a retail store is a 2PL provider. Their job is to move products from one location to another.
Freight forwarders, on the other hand, don’t own transportation equipment. Instead, they act as intermediaries between businesses and carriers. A freight forwarder organizes shipments by finding carriers, booking transportation, and handling paperwork. For instance, a freight forwarder might arrange for a shipment to travel by truck, ship, and plane to reach an international destination.
The main difference is that 2PLs own the vehicles they use for shipping, while freight forwarders focus on coordinating transportation logistics. Businesses typically use freight forwarders for complex or international shipments and 2PLs for simple, direct deliveries.
Freight Forwarding vs. 3PL
The biggest difference between freight forwarders and 3PLs is their range of services. Freight forwarders specialize in transportation logistics. They arrange goods shipped by air, sea, rail, or road. While they help businesses move products efficiently, they don’t offer additional services like warehousing or order fulfillment.
A 3PL, on the other hand, manages multiple parts of the supply chain. They organize transportation, store products, pack orders, and handle returns. For example, a 3PL might keep a company’s inventory in its warehouse, pack orders as they come in, and ship them directly to customers. This makes 3PLs a better option for businesses that want a more complete logistics solution.
Freight forwarders are ideal for businesses that only need help with shipping, especially for international deliveries. A 3PL is a better fit for companies that want to outsource logistics tasks beyond transportation.
Freight Forwarding vs. 4PL
Fourth-party logistics (4PL) providers take logistics outsourcing a step further. Unlike freight forwarders or 3PLs, a 4PL acts as a consultant and manages the entire supply chain. They don’t directly handle transportation or warehousing but oversee multiple logistics providers to ensure smooth operations.
For example, a 4PL might hire a freight forwarder to arrange international shipping, a 3PL to store and fulfill orders, and a 2PL to handle local deliveries. The 4PL ensures that all these providers work together efficiently, giving the business a single point of contact for its logistics needs.
The difference between a freight forwarder and a 4PL lies in their focus. Freight forwarders organize shipping, while 4PLs coordinate all aspects of the supply chain. A 4PL is ideal for large companies that want a partner to oversee every part of their logistics strategy.
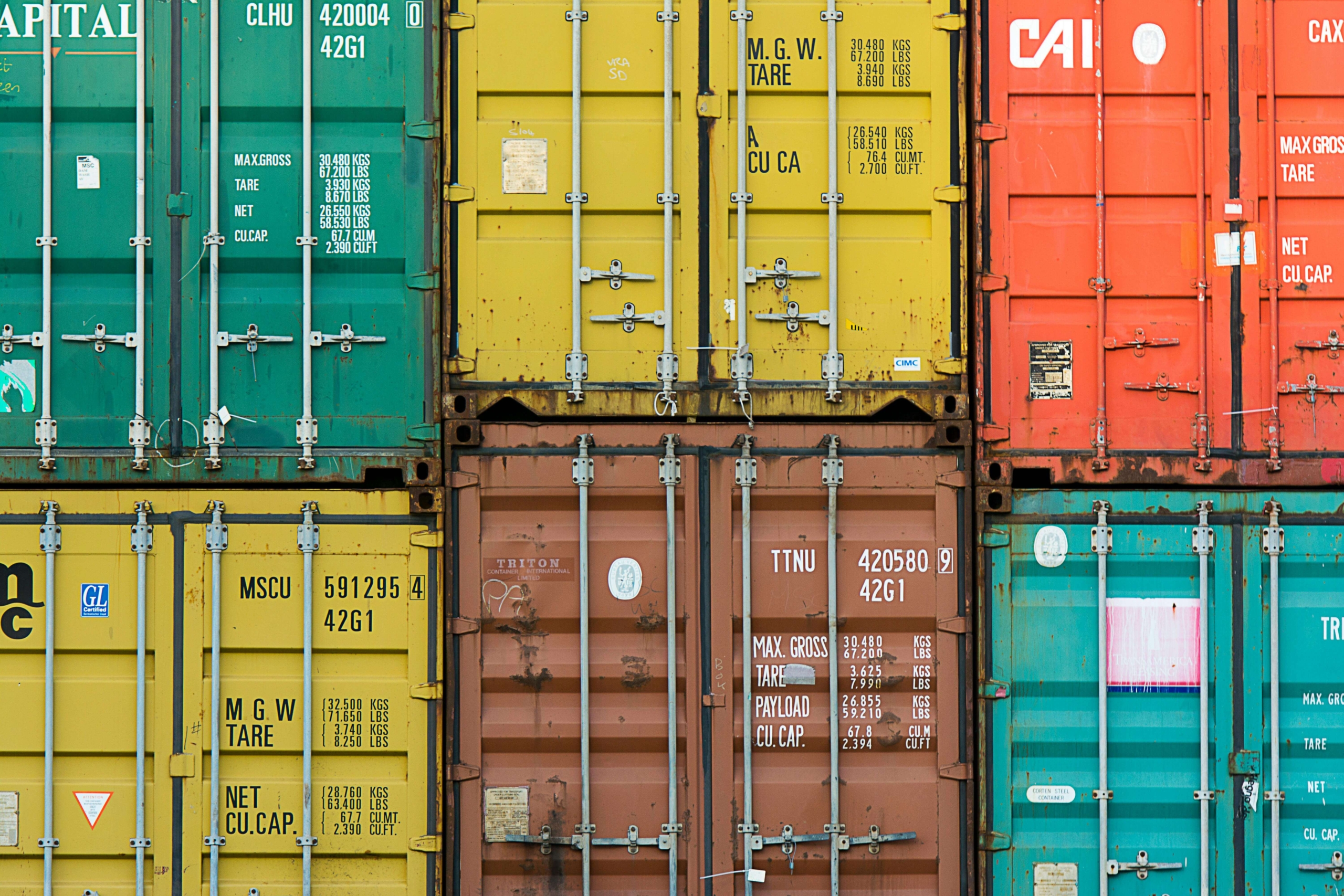
Who Should Work With a 3PL Provider?
Third-party logistics (3PL) providers are valuable partners for many businesses. They help manage logistics tasks like storing products, packing orders, and shipping them to customers. While any business can benefit from a 3PL’s services, some businesses may find it essential to work with one.
Companies with high order volumes, limited storage space, or fluctuating demand often need 3PL support to meet their supply chain needs. Businesses offering fast shipping options also rely on 3PLs to meet customer expectations. Let’s look at specific situations where working with a 3PL can make a big difference.
Fulfilling High Daily Order Volumes
Businesses that handle large numbers of orders every day can benefit from a 3PL. Managing high volumes of orders can be overwhelming, especially for companies without enough staff or systems to keep up.
A 3PL helps by streamlining the fulfillment process. They use warehouses to store inventory and technology to manage orders efficiently. When a business receives an order, the 3PL handles picking, packing, and shipping, saving time and reducing errors. For example, an online retailer with hundreds of daily orders might rely on a 3PL to process and ship them quickly.
High-volume order fulfillment also requires consistency and accuracy. Mistakes, like shipping the wrong product or missing an order, can lead to unhappy customers. 3PLs use systems that reduce errors and improve accuracy. This ensures businesses maintain a good reputation and satisfy customers, even as order volumes grow.
Running Out of Inventory Storage Space
For businesses that struggle to find room for their inventory, working with a 3PL can solve the problem. Storing products takes up space, and as businesses grow, they may outgrow their storage facilities. Expanding storage on their own can be costly and time-consuming.
3PLs provide access to large, well-organized warehouses where businesses can store their products. These warehouses are designed to handle all kinds of inventory, from small consumer goods to bulky equipment. By using 3PL’s storage facilities, businesses can free up space in their buildings and avoid the cost of building or renting additional storage.
Another advantage of using a 3PL for storage is their ability to manage inventory efficiently. They use tools like inventory management software to track stock levels and send alerts when products run low. For example, a clothing store might use a 3PL warehouse to store seasonal products and avoid running out of popular items during busy times.
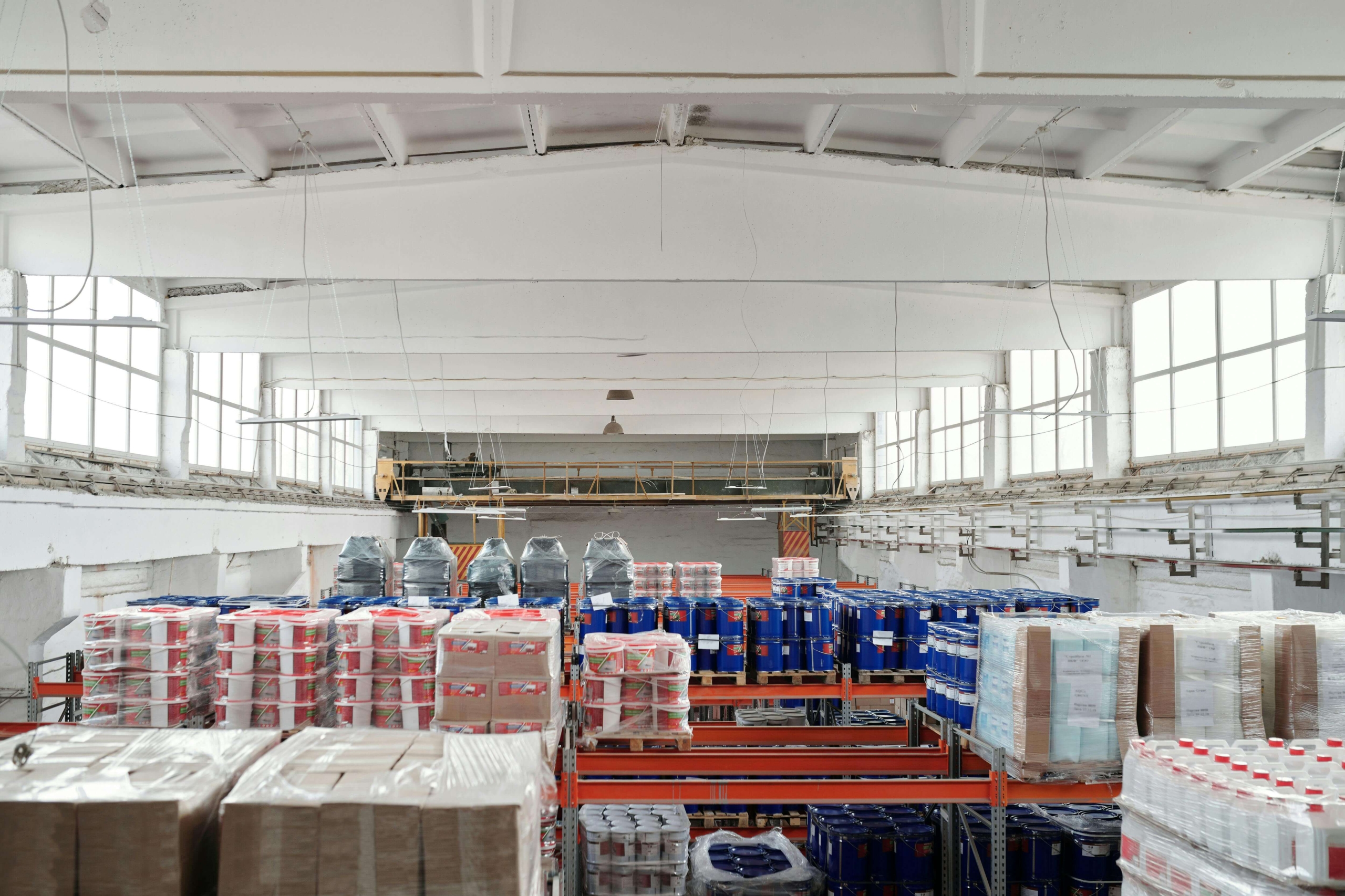
Managing Spikes in Customer Demand
Businesses that experience sudden increases in customer demand often turn to 3PL providers for support. Spikes in demand can happen during holidays, sales events, or product launches, and during these times, businesses might struggle to fulfill orders on their own.
3PLs help by providing extra capacity during busy periods. They have the staff, space, and systems to handle higher order volumes. For instance, an e-commerce business might see a large spike in orders during Black Friday or Cyber Monday. A 3PL can manage the surge by processing and shipping orders quickly, ensuring customers receive their purchases on time.
After the busy period ends, the 3PL scales back its operations, so businesses don’t have to worry about unused space or extra staff. This flexibility allows businesses to handle demand spikes without overcommitting resources.
Offering Expedited Shipping Options (e.g., 2-Day Delivery)
Fast shipping is becoming a standard expectation for many customers, especially in e-commerce. Businesses that want to offer expedited shipping options, like 2-day delivery, often need the help of a 3PL.
A 3PL makes fast shipping possible by using strategically located warehouses near major shipping hubs, which reduces transit times. For example, a business might store its products in multiple 3PL warehouses nationwide. This allows the 3PL to ship orders from the warehouse closest to the customer, ensuring faster delivery.
In addition to location, 3PLs work with reliable carriers to ensure orders arrive on time. They also handle the logistics of planning delivery routes and tracking shipments. By partnering with a 3PL, businesses can provide fast, reliable shipping without building their logistics network.
Expedited shipping improves the customer experience and gives businesses a competitive edge. With the help of a 3PL, businesses can meet customer expectations for speed while keeping costs under control.
Benefits of 3PLs
Third-party logistics (3PL) providers offer many benefits to businesses of all sizes. By outsourcing logistics tasks like storage, shipping, and inventory management, companies can improve efficiency, save money, and provide better customer service.
Working with a 3PL allows businesses to expand their operations and reduce in-house logistics challenges. Let’s explore some key benefits of partnering with a 3PL.
Expansion Into New Markets
A major advantage of working with a 3PL is expanding into new markets. Businesses looking to grow often face challenges like managing shipping costs, navigating customs regulations, or finding the right carriers. A 3PL helps solve these problems by providing expertise and resources for reaching customers in different locations.
For example, a business entering the international market might rely on a 3PL to handle customs paperwork and ensure packages meet local regulations. The 3PL can negotiate better shipping rates and coordinate deliveries, making the process more affordable.
Domestically, 3PLs can use strategically located warehouses to ensure fast delivery to new regions. Businesses can reduce transit times and shipping costs by storing products closer to customers, which gives them a competitive edge, especially in markets where fast delivery is a priority.
Optimized Warehouse Space
Managing warehouse space can be expensive and time-consuming, especially for growing businesses. A 3PL provides access to large, efficient warehouses, eliminating the need for businesses to invest in their storage facilities.
3PL warehouses are designed to store a wide range of products. They use tools like inventory management systems to keep track of stock and ensure items are easily located. For example, a 3PL might use barcode scanners to track items moving in and out of the warehouse, reducing errors and improving efficiency.
By outsourcing warehousing to a 3PL, businesses can avoid running out of space or paying for more storage than they need. Instead, they can scale their storage use up or down based on demand. This flexibility helps businesses save money while ensuring they always have the needed space.
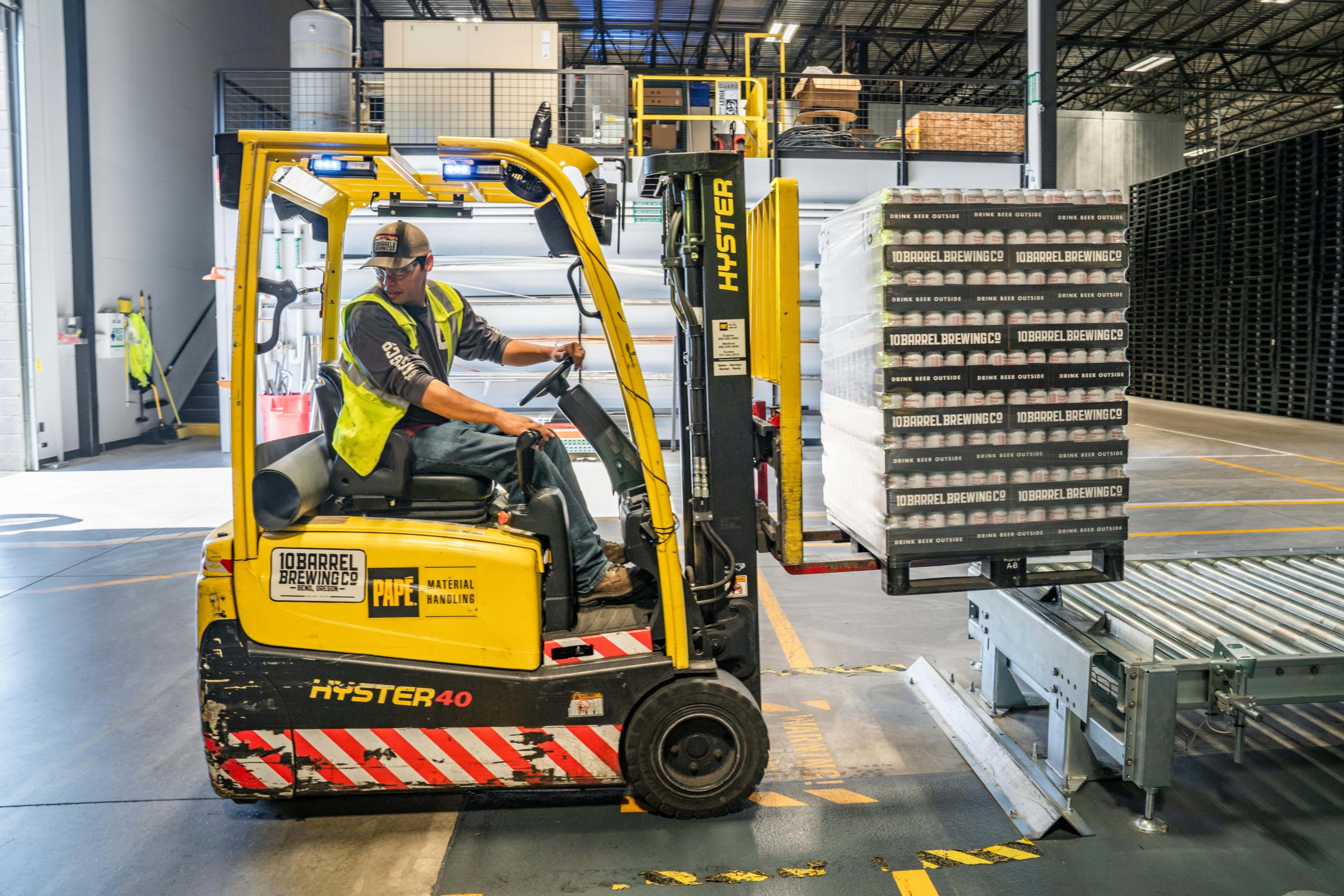
Lower Overhead Costs
Using a 3PL can significantly reduce overhead costs. Managing logistics in-house requires businesses to invest in warehouses, staff, technology, and equipment. These expenses can add up quickly, especially for small or medium-sized businesses.
A 3PL spreads its costs across multiple clients, allowing businesses to access high-quality logistics services at a fraction of the cost. For example, a business can rely on the 3PL’s existing staff and systems instead of hiring a full team to manage inventory and shipping.
Lower overhead costs mean businesses can use their resources in other areas. They can focus on growth, such as developing new products or marketing to new customers. By partnering with a 3PL, businesses save money while still maintaining a reliable and efficient supply chain.
Challenges of 3PLs
Third-party logistics (3PL) providers offer many advantages. Yet, businesses may face some challenges when working with them. Being aware of these challenges can help businesses prepare and avoid potential issues.
Upfront Investment Requirements
Partnering with a 3PL often involves upfront costs. These costs may include setting up new systems or transferring inventory to 3PL warehouses. Don’t forget about expenses related to training employees on how to use the 3PL’s processes. For smaller businesses, this can feel like a big expense.
For example, connecting a business’s order system to a 3PL’s software might require hiring IT support or buying new tools. Businesses also need to pay for services like storage and shipping before they see the benefits of outsourcing.
Although these upfront costs seem high, they usually lead to long-term savings. By budgeting for these expenses, businesses can make the transition smoother and more affordable.
Adapting to New Workflows
Switching to a 3PL means learning new ways of doing things. Businesses must adjust to the 3PL’s systems, which may differ from their old processes. This can take time and effort, especially during the first few months.
For example, a business might need to use the 3PL’s inventory system to track stock or follow its rules for processing returns. Employees may need extra training to understand these new workflows.
Good communication is key when working with a 3PL. The business and the 3PL must stay in touch to ensure orders are accurate and on time. Clear communication helps reduce mistakes and keeps customers happy.
The adjustment period can be challenging. Yet, businesses often find that the benefits of using a 3PL outweigh these initial hurdles.